Sri Devaraja Agro Industries based at Krishnagiri is one of the leading mango pulp manufacturer in Tamilnadu. With a manufacturing capacity of over 350 MT’s per day they also process Tomato, Guava, Papaya, Pineapple etc.
Alphonsa, Sendura, Neelam and Totapuri are the common mango varieties used in pulp making. Of them, ‘Totapuri’, which is cultivated in 70 per cent of the district, is the most preferred for pulp production. Mangoes are cultivated in about 45,000 acres of land.
In Tamil Nadu there are nearly 400 food processing units of which nearly 80% belongs to the category of small-scale units. The remaining units are in the medium scale category with an average production capacity of 80 tonnes per day.
Mangoes are seasonal fruits and are not available throughout the year and they cannot be preserved in the original form for long. To have the pleasure of tasting the mango virtually in every drop without losing its taste, flavour and colour at all times must have been a distant dream once, but it is a tasty reality now. Thanks to the state of art mango pulp processing initiatives run by the entrepreneurs who function with a vision and mission keeping quality as their life breath.
Production pipeline of mango pulp industry @ Sri Devaraja Agro, the Leading Mango Pulp Manufacturer in Tamilnadu:
SORTING
A Group of 10 to 20 workers segregate ripe and unripe fruits from the lot. Unripe fruits are kept aside in a separate lot to ripen in the near days and the ripened fruits are carried by the workers to be put on the conveyor belt to be taken for production.
CONVEYOR BELT
Nearly 1000 tonnes of mangoes are sorted out in a day and the ripe fruits are fed to the conveyor belts.
A few workers stand on either side of the conveyor belts to ensure that only good ripened fruits move on the conveyor and remove any decayed or un ripened fruits found on the conveyor.
WASHING MACHINE
The ripened fruits move on the conveyor belt and reaches washing machine.
CHLORINE TANK
It is being thoroughly washed in the water mixed with chlorine to remove the bacteria from the skin.
DIPPING IN THE NORMAL WATER
They are again dipped in the normal water and thoroughly cleaned again and fruits are then sent to the next stage.
CUTTING CONVEYOR
Mangoes thus cleaned with fresh water are then sent to cutting conveyor. On each side of the conveyor belt nearly 30 persons engage in removing the stem attached to the fruits. In addition to this, any damaged fruits if found will also be removed at this stage. These food grade fruits are moved to the next stage called De – stoner through the 40 feet food grade conveyor belt.
DE- STONER
In the De-stoner the outer skin and the hard seed are separated. The pulp from the fruits gets collected in a tank.
De-Stoner is the wonder machine which extracts only the pulp leaving aside skin and the hard mango nut.
The pulp thus collected in the tank is sucked through the screw pump and flows through the SS pipes to reach the pulper.
PULPER
This two-in-one pulper has the capacity of 5 tonnes. Filters made up of wood and nylon materials are fitted in this. The process of filtration of the pulp takes place here. Fruit fibers and other dross in the pulp are removed at this stage.
Pure fruit pulp is then collected in a tank called finisher tank. The pulp collected in this tank is ready for process. This pulp is normally called cold pulp.
PRE – HEATER TANK
The cold pulp will be sent to the holding tank before heating.
Cold pulp is being sent through SS Pipe to the equipment called Pre-Heater. Here the pulp is heated making use of steam by providing 60 ‘to 70 ‘centigrade of heat.
The heated pulp is then collected in the collection tank.
This pulp is again sent to the De-Canter machine for removing dross which appear in the pulp as black and brown specs.
Dross free, bacteria free, pure mango pulp is ready and it is received in the collection tank.
The pulp from the collection tank is pumped to the sterilizer and initially the pulp is heated up to 110 ‘centigrade with help of steam which flows in the reverse direction.
Subsequently the pulp is sent to the cooling module. In this cooling module the temperature of the hot pulp is stabilized to 28 ‘to 30 ‘centigrade with the help of chilled water which flows on the reverse side of the module. This effect of heating and subsequent cooling provides with the pulp free from lively organisms.
Entire quality control process is totally mechanized and controlled by the technicians who operate on the computer panel attached to the sterilizer.
Finally, the pulp reaches the filling head. In the aseptic bars which are thoroughly sterilized using steam. The pulp is being filled untouched by human hand conforming to international standards.
The pulp is filled in Aseptic Bags to around 210 to 215 kgs kept in the drums and sealed. The filled drums are moved to the warehouses and put on the lots and kept pending for shipment till the advice of the buyers.
Efficient management; Enthusiastic workers, quality conscious professionals have provided the dynamism of success to this enterprise.
SRI DEVARAJA AGRO INDUSTRIES
Leading Mango Pulp Manufacturer in Tamilnadu
Metpenda, Kothapatta Village,
Krishnagiri – 635001
Tamilnadu, India
Phone: +91 4343 231116, 230231
Mobile: +91 98427 44190
Fax: 04343 231617
info@sridevarajaagro.com / shridhevaraj@yahoo.co.in
You may also be interested in this manufacturer of mango pulp:

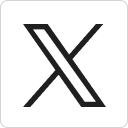




2 thoughts on “Sri Devaraja Agro”