Intelligent Micro System Pvt. Ltd (INM) specializes in microprocessor/microcontroller-based control systems with electro – pneumatic controls especially for hazardous area applications such as LPG bottling plant controls, explosion proof / Intrinsic safe weighing systems and on-line equipment. In addition, INM makes standard industrial PLC controllers for various industries such as automobile, tool making, textile, electrical, switch gears etc.
Incorporated in the year 1991, Intelligent Micro System Pvt. Ltd. (INM) is promoted by two technocrats Er. K. Vijaykumar M.E., FIE and Er. K. Prabakar M.E. The promoters are post graduate engineers, the former in electronics engineering and the latter in mechanical engineering, both with management qualifications and over 36 years’ experience in the field of Industrial automation.
The Company offers turnkey solutions for LPG bottling units right from conceptualization, need based design, development, manufacturing, supply, erection, commissioning, training, on-line and off-line technical / maintenance and spares support thus taking care of the needs of the customers fully.
Their product range includes:
- Stationary Filling Systems
- Electronic Carousel Filling
- Online Main Equipment
- Other Plant Equipment
- Container Filling Plants
- Conveyors, Controls & Parts
- Mobile LPG Bottling Plant
- LPG Bottling Plant Controls
STATIONARY FILLING SYSTEMS
- Dual Filling M/cs. Of 5Kg to 47.5Kg Cylinder filling capacity on roller conveyor
- View of standalone Filling M/c.
- Semi-automatic Batch Filling system with conveyors
ELECTRONIC CAROUSEL FILLING EQUIPMENT
- 24 M/c. CAROUSAL FILLING Unit
- CAROUSAL Master controls
- 6 M/c. of 12 M/c. frame CAROUSAL
ONLINE MAIN EQUIPMENTS
Automatic Check weigh System
This station accepts data from carousal or filling machines and automatically allows one cylinder at a time into the check weigher after which the line stopping unit closes. The cylinder gets automatically lifted from the conveyor and if data is available, will find the weight difference based on the cylinder type and tare weight and display the difference. If the difference is beyond range allowed, the cylinder is then lowered and rejected by the pusher system automatically. If data is not available, operator is prompted to enter the tare weight after selecting the type of cylinder. The capacity is up to 1500 cylinders per hour depending on conveyor speed. The display shows the total cylinders handled, no. of overweight cylinders and no. of underfilled cylinders.
Automatic Weight correction System
This station allows one cylinder at a time into the system and closes the line stopping unit and prompts operator to enter the tare weight after selecting the type of cylinder. Then it lifts the cylinder and weighs it to determine if it is an overfilled cylinder or an underfilled cylinder. If it is an overfilled cylinder, the machine will tilt the cylinder after switching on the evacuation line and once the weight becomes less, it will come back to vertical after switching off the evacuation line and then switch on the filling line to top up the gas if any to weigh correctly and then lowers the cylinder to the conveyor automatically. If it was an underfilled cylinder, the filling line gets actuated to top up the cylinder to the correct weight and lowers the cylinder to the conveyor. Capacity 30-100 cylinders per hour. The display shows the no. of cylinders handled.
Automatic Valve testing system
This station allows one cylinder at a time into the machine and immediately connects itself to the valve and checks for O-Ring defect and Valve leak defect after which it releases the cylinder down line. If it is and O-Ring defect cylinder, it will reject it to the O-Ring line with the pusher and if it is a valve leak cylinder, it will reject the cylinder to the valve leak line through its pusher. The display will show the status viz. O-Ring leak or Valve leak or Okay cylinder and also can show the total cylinders, OK cylinders, VL cylinders and O-Ring defect cylinders. The capacity is up to 1500 cylinders per hour depending on conveyor speed.
OTHER PLANT EQUIPMENTS
- Inline washing and drying unit direct from unloading conveyor complete with water pump and air blower.
- Inline civil type test water bath for operator to check for bung and body leaks of any cylinder on the conveyor.
- Two-cylinder pneumatics-controlled dip type bath for checking bung body leaks of cylinders.
- Vacuum pump for purging station.
- Manual pneumatic assisted valve changing station.
MOBILE LPG BOTTLING PLANT
- Mobile Bottling Plant model I: with 8 Ton LPG: Capacity ~ 550 cylinders per trip
- Mobile Bottling Plant 2 truck Model II with LPG tanker & Filling cabin on LCV. Capacity: 800 cyl.per trip
- Mobile Bottling Plant Model III: with DG & Air compressor and connected to standard LPG tanker.
- Mobile Bottling Plant Model IV: Filling cabin on Single axle trailor and connected to standard LPG tanker
- Mobile Bottling Plant Model V: Filling cabin on Double axle trailor and connected to standard LPG tanker: Capacity limited by external standard tanker
CONTAINER FILLING PLANTS
- Container filling machine
- Filling container unit
- LPG Pump air compressor
- Container Filling Plant Boltable at civil platform at site and connected to external power minimum 15 Meters away and any standard LPG tanker can be connected to the LPG inlet of container for filling. Has 2 electronic intrinsically safe Filling machines, Check weigh cum Electronic Valve testing station and has built in LPG Pump and air compressor.
CONVEYORS, CONTROLS & PARTS
- Typical 2-line conveyor integrator with divertor
- Twin arm Line stopping unit
- Standard Filling gun with spring return
- IMUC: Intrinsically safe Universal Electronic controller
- Flameproof & Explosion proof Power supply units housing zener Barriers
- IMUC Control card
- Solenoid valves
- Load cells & limit switches
OTHER PRODUCTS:
- Electronic Market Return Checking System (CVT cum Check Weighing System).
- Electronic SQC system.
- Auto O-Ring Checking system.
- Standard and Specialized Chain conveyors & Roller conveyors.
- Filling Guns, CVT & EVT Guns.
- Line control Stoppers.
- Pneumatics Controlled Pushers and Pullers.
- Cylinder Evacuation Systems
- Auto-Purging System.
Intelligent Micro System Pvt. Ltd., LPG Bottling Plant Controls
No: 14, Block II,
Sidco Electronic Complex,
Thiru-Vi-Ka Industrial Estate,
Guindy, Chennai – 600032, Tamilnadu India.
+91 44 2250 0917, 2250 0193
info@inmltd.com
You may be interested in this conveyor manufacturer:

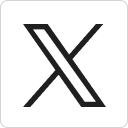




One thought on “Intelligent Micro System”