LGB is a premier manufacturer of sprockets, automotive chains, brake shoes, timing chains, timing belts, belting tensioners, drive belt tensioners etc.
The company has 17 chain manufacturing plants, all ISO 9001 certified by Underwriters Laboratories Inc., USA. Three of the manufacturing facilities along with the central functions have been registered to ISO/TS 16949 by UL, USA.
- The first chain manufacturer in India to be awarded the ISO 9001 certification.
- Recognized Export House – about 10% of LGB’s products are being exported to USA, European countries, Australia, New Zealand, South Africa, Japan, Far & Middle East countries.
- Technology upgradation done on a regular basis to stay in tune with the latest trends.
- On-going training programs to update information and processes.
- Product acceptance both in India and abroad.
Transmission Products
Automotive Chain
- Motorcycle and Moped Drive Chains
- Agricultural Chains – Heavy Duty
- Timing Chains / Engine Mechanism Chains
- Automotive Kits
Sprockets
LGB produces about 10 Million sprockets per annum for various applications, mainly for Motorcycle Drive System.
Drive sprockets are Fine Blanked and case hardened for highest precision, accuracy and wear resistance.
Rear Wheel sprockets are hobbed and zinc plated for rust prevention. For Special application, rear wheel sprockets are also fine-blanked and induction hardened.
For Motor cycle and Mopeds, LGB supplies chains and sprockets in a kit form for OEMs and After market.
Tensioners
Timing chain tensioners will improve the operation of chain drives by keeping the tension constant. Because the tensioners are effective in
- reduction of noise
- uniform & more efficient transmission of drive torque
- decreasing wear
- extending life of chains
These units are easy to install & maintenance-free. The spring-loaded units, available in rotational & movement types, will automatically keep the tension constant, eliminating frequent manual adjustments that would interrupt the operation of the machinery.
All tensioners should be installed on the slack side of chains. It is also recommended, for all tensioners, that the tension force be applied from the outside of the chain loop as to not reduce the wrap-around angles of the chain over the sprockets.
Function of Tensioners
The function of the tensioner is to give & maintain proper tension to the chain. The tensioner does not slip back but will move forward for ideal chain tension as the chain elongates. Whether Plunger-type or any other, tensioners prevent chain whipping, back lash & allow timing chain to attain its maximum working life.
Belts
Rolon Raw edge cogged belts are the result of extensive research and development. It has the unique distinction of being the first Indian manufacturer to be certified ISO 9001 for cogged belts and chains.
They have been fabricated for more efficient transmission and with low stretch characteristics.
The cogged belts have unique rubber components and imported raw materials which ensure maximum resistance to heat and wear-and-tear. LGB has also strong footholds in the manufacture of timing belts and variable speed belts.
Rolon cogged belts find themselves in diverse automotive application like mopeds, LCV/s, cars/jeeps, 3-wheelers, trucks and tractors.
TIMING BELTS / VARIABLE SPEED BELTS
COGGED BELTS
POLY ‘V’ BELTS
- Longer life with low stretch capabilities
- High power capacity
- Less vibration
- Better Drive ratio flexibility.
Application:
For Automotive 2wheeler, 3wheeler, Car, LCVs, Trucks and Tractors Applications.
Brake Shoe
Rolon brake shoes are Manufactured with safety and reliability as the prime criteria. The brake shoes are made out of high grade Aluminium alloys for pressure die casting and under close quality supervision. The brake Linings are made out of specially formulated friction material to achieve instant braking function and longer life. The brake linings are made with both asbestos and asbestos – free material. The range covers brake shoes for mopeds, scooters and motor cycles.
Salient features
- Consistent Co-efficient of friction
- Heat resistant for total working range
- Low noise at varying applications
- Stable performance for assured safety
- Sensitive braking
- Appropriate hardness
- Excellent stopping power
- Durable and anti wear & tear
- Eco –friendly
Research & Development
The world class Research and Development facilities available for testing and development of roller chains and silent chains in LGB has been utilized to develop and test the brake shoes in co-operation with experts in friction material technology. As brake shoes plays vital role in the safety of the rider and vehicle no effort has been spared from selection of raw material, design of process and manufacturing controls The manufactured products are tested for its quality and reliability.
New products are developed periodically, subjected to stringent laboratory evaluation and finally tested on vehicles extensively. We have the unique distinction of having zero failure rate, repeat order for new development in OEMs, exports and aftermarket.
The companies R&D has the following facilities and also employs facilities outside to test brake shoes.
- Raw Materials testing Laboratory
- Chase COF dynamometer
- Hardness testing machines
- Universal testing machines
- Dry friction material testing machines
- Co-ordinate measuring machines
- CVT testing machines
- Salt spray testing machines
Other Friction Products
Other than brake shoes Rolon range covers clutch plates, brake pads and clutch shoes manufactured with same philosophy.
Metal Forming
Fine Blanking
Fine blanking is a one hit production process for precision sheet metal parts. When the need is to manufacture high quality components with better flatness, surface finish, better dimensional tolerances, the solution is fine blanking.
Unlike conventional methods like casting, forging, chip removal machining etc. there is no need for secondary operations like milling, grinding, drilling etc, what’s more, the part processed is ready for assembly immediately.
Fine blanking gives you the power of versatility. Creative design solutions like bending, semi-piercing, countersinking, deep drawing etc are possible by combining cold forming with fine blanking.
LGB is fully equipped to meet your demands for both fine blanking and creative forming so that you get the advantage of cost savings, reduced process time, fast operations and course parts that are of outstanding dimensional, flatness and shape accuracy.
Fine blanking works through total precise process control. This is done through a coordinated action between a triple action fine blanking press (separate regulation facility for total pressure, v-ring pressure and counter/ejection pressure) and a fine blanking tool. The fine blanking tool is a specially designed complete press tool with a v-ring and an extremely small die clearance. LGB brings to bear its expertise in all areas of operation right from process metallurgy and tool engineering to press design, to give customers the very best in fine blanking.
Machined Components
Forging
COLD FORGING
During 1990, LGB ventured into Cold Forging of Rollers for its captive consumption and today LGB is the leading manufacturer of quality Cold Forging Rollers.
In 2000, the division pioneered the manufacturing of Steering Suspension Linkage parts such as Ball Rods, Ball Pins, Ball Sockets etc, by Cold Forging Process in vertical / mechanical and Hydraulic presses in India.
LGB Forging Division comprises the most advanced state-of-the-art infrastructure available for Tool designing and manufacturing.
This division is equipped with full fledged testing equipments and facility.
LGB has sophisticated Integral Quench Furnaces installed for accurate and consistent heat treatment of various forged components, supported by most modern metallurgical facility, where Cold Forged Products are heat treated to stringent specifications to customer satisfaction.
To back this extensive and modern infrastructure, LGB has the best of Human Resource Pool consisting of a dedicated core team of experts having vast experience and skills in forging.
All these, coupled with LGB’s expertise in sourcing the right quality of raw materials and pre-processing ensures the quality of the product at all stages.
HOT & WARM FORGING
Apten Forgings is a subsidiary of the LGB group specializing in the manufacture of high-quality close tolerance press forgings. This unit is one of the most modern forging plants in India having the state-of-the-art KURIMOTO C2F 1600 ton forging press and a 1000 ton HASENCLEVER forging press. The various tooling are designed in-house and built with special emphasis on consistent quality using advanced CNC machines.
Apten Forgings strictly adheres to the norms of international standards and specifications, the unit has set in place sophisticated Quality Control measures backed by stringent quality control checks at every stage of production – Right from the raw material sourced to the finished products.
The highly specialized press forging products are used as critical application products in auto electricals and transmission parts of two and four wheelers.
At Apten Forgings, continuous development is a part of life and customers are provided with the best service always.
Hot / Warm forging plant located at Bangalore has been certified with QS9000 by UL, U.S.A. The products from this division are being supplied to critical application in auto electrical, transmission parts of two & four wheelers.
Special Features :
- Outstanding manufacturing technology and equipment.
- High-dimensional accuracy.
- Stringent quality checks at every stage of manufacture.
- Adoption of high standards in the selection of raw material, commensurate with applications.
Facilities :
- 1600T high speed “KURIMOTO C2F-1600” forging press.
- 1600T Chin Fong Warm Forging Press line.
- 1000T ton “HASENCLEVER” forging press.
- 650T Hydraulic Cold sizing Press .
- 500T “ERFURT” billet shear
- 400T coining press
- 250T trimming press
- 250 KW Newelco induction billet heater
- 1Tonne/hr billet heating furnace
- 500 kg / hr billet heating furnace
- Magnaflux crack detection equipment
- Ultrasonic testing equipments
COLD HEADING
It is a process of set of punches in a forming die to get a required shape.
Being done without any warming on the raw material.
Can have high precision components and high productivity out of this machine.
Wire Drawing
This Division has the capacity for Wire drawing of 200 tonnes and flattening of 225 tonnes per month.
Around 60% is being used for LGB’s own use and the rest is supplied to other Chain Manufacturing Plants, Spring Steel Suppliers, Umbrella Manufacturers etc.,
We also supply in Triangle or Trapezoidal shape as per customer requirement.
L.G.Balakrishnan & Bros. Ltd.,
Krisnarayapuram Road, Ganapathy,
Coimbatore – 641 006.
0091 422 253 2325
0091 422 253 2333
info@lgb.co.in
http://www.lgb.co.in/index.html
You may also be interested in this manufacturer:
Sprockets
Sprockets
Sprockets
Sprockets
Sprockets

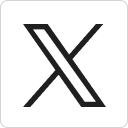




2 thoughts on “LGB & Bros”