MEPCO entered the building and construction industry in 2015, manufacturing AAC blocks and AAC panels under the brand name “MEPCRETE”. The company has India’s biggest manufacturing plant at SIPCOT, Thiruvallur district, near Chennai, Tamilnadu with a production capacity of 30,000 cubic meters per month. The AAC blocks they manufacture are fabricated using the finest quality of fly ash to ensure their durability, reliability, and eco-friendliness.
AAC Blocks
AAC stands for autoclaved aerated concrete. AAC blocks are the new favorite building material of the construction industry
These blocks are lightweight, energy-efficient, fire-resistant, and excellent thermal insulators. The blocks are extremely lightweight and thus suitable for internal as well as external construction.
Aerated concrete blocks are ideal for all kinds of structures such as schools, hospitals, hotels, offices, independent housing, and apartments. The buildings constructed with AAC blocks are also known as environmentally friendly buildings and these buildings don’t require curing and plastering.
AAC was developed in 1924 by a Swedish architect, who was looking for alternate building material with properties similar to that of wood – good thermal insulation, solid structure, and easy to work with.
Autoclaved Aerated Concrete blocks are manufactured by recycling fly-ash. Fly ash is mixed with cement, lime, water, and an aerating agent.
Why Use AAC Blocks?
- Energy saving
- Easy to install
- Less weight
- Endurance
- Precision
- Non toxic
- Thermal insulation
- Fire resistance
- Acoustic performance
- Moisture resistance
- Workability
- Cost saving
- Fast construction
- Water barrier
- Fire resistance
- Earthquake resistant
- Reduce plaster cost
- High strength
- Pest resistant
AAC Blocks Cost Saving & Benefits
Reduces overall construction cost by 30%”
- AAC blocks are the best alternative to other building materials such as steel, cement and jelly.
- High-insulation blocks save up to 30% in energy costs. Reduces construction time by 20%
- Reduces operating cost by 30-40%
- No burning of fossil fuel (Coal)
- No emission of Carbon Di-Oxide (Co2)
- Steam cured cement blended blocks
- Superior thermal insulation of the blocks reduces the need to turn on the air conditioner which in turn helps in saving electricity costs.
- Reduces overall construction cost by 30% as it requires less jointing and reduces need for cement and steel.
- Helps in saving unnecessary labour costs
- Reduces overall labour and material costs
- The blocks maintain ecological stability
- No top soil cutting which saves precious land
AAC Manufacturing Process
Autoclaved Aerated Concrete blocks are manufactured by recycling fly-ash, a waste generated from thermal power plant. Fly ash is mixed with cement, lime, water and an aerating agent.
When AAC is mixed and cast in forms, several chemical reactions take place that gives AAC its lightweight and thermal properties. Aluminum powder reacts with calcium hydroxide and water to form hydrogen. The hydrogen gas foams and doubles the volume of the raw mix creating gas bubbles up to 3mm in diameter. At the end of the foaming process, the hydrogen escapes into the atmosphere and is replaced by air.
This process requires 30% less energy compared to clay brick manufacturing. When the forms are removed from the material, it is solid but still soft. It is then cut into either blocks or panels, and placed in an autoclave chamber for 12 hours. Because of the relatively low temperature used AAC blocks are not considered fired brick but a lightweight concrete masonry unit. After the autoclaving process, the material is ready for immediate use on the construction site.
AAC Blocks Comparison
Parameter | MEPCRETE AAC Block | Concrete Block | Clay Brick |
Size (mm) | (600x200x100-300) | (400x200x100-200) | (230x115x75) |
Variation in dimensions | +/-1mm | +/-3mm | +/-5mm |
Compressive strength | 30 – 50 kg/cm2 | 40 – 50 kg/cm2 | 25 – 30 kg/cm2 |
Dry Density | 550 – 700 kg/m3 | 1800 kg/m3 | 1950 Kg/m3 |
Fire Resistance | 4 – 6 Hour’s Depending on thickness | 4 hours | 2 hour |
Sound Reduction Index (dB) | 60 for 200 mm thick wall | 30 for 200 mm thick wall | 40 for 230 mm thick wall |
Thermal Conductivity W/(K-m) | 0.122 | 0.51 | 0.81 |
AAC Block Advantages
Light Weight
It is four times lighter than traditional bricks.
Cost-Effective
Reduces operating costs and overall construction costs.
Fire resistant
Non-combustible & can withstand 6 hours of direct heat exposure.
Better Sound Insulation
Excellent acoustic insulation.
Accuracy In Size
High dimensional accuracy, available in exact sizes. Requires no thickset mortar.
Faster Construction
Reduces construction time by 20%. Easy to install. Constructing with AAC is very rapid
Energy Saving
The low thermal conductivity of AAC blocks ensures better thermal energy efficiency.
Longer Life
Durable, high compressive strength & termite resistant. Requires no plastering or curing.
Low water absorption
The water absorption of AAC blocks is relatively lower than others.
Earthquake Resistant
Lightweight AAC blocks reduce the impact of an earthquake on a building.
Environmental friendly
Manufactured using recyclable industrial waste material named fly ash.
BIS Norms
Manufactured as per BIS Norms.
Highly Insulating
Excellent thermal insulation. Higher savings on heating and cooling costs.
High Workability
Blocks can be easily cut, drilled, nailed, milled & grooved. Excellent size/weight ratio.
Marketing Office
THE METAL POWDER COMPANY LIMITED – AAC UNIT,
26 & 27, Poonamallee High Road, Periamet,
Chennai 600 003.
Corporate Office
THE METAL POWDER COMPANY LIMITED – AAC UNIT,
Maravankulam, Thirumangalam – 625 706. Madurai Dt., Tamilnadu, India.
Ph : +91-4549-280599, 9843899390, 9843862146
Fax : +91-4549-280689
Factory
THE METAL POWDER COMPANY LIMITED – AAC UNIT,
A-10, Sipcot Industrial Park, Thervoy Kandigai,
Periapalayam to Uthukottai High way road,
Gummidipoondi Taluk, Thiruvallur District,
Chennai, Tamilnadu, India. Pincode – 601 202.
Phone: 7604956669, 7604956661
http://www.mepcrete.co.in/index.php
You may also be interested in this AAC brick manufacturer:

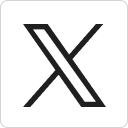




One thought on “MEPCO AAC Unit”