Established in the year 1999, G.S.Machineries‘ equipment portfolio includes Sand casting equipment, Aluminium casting equipment, Surface blasting (sand blasting machinery), Band Saws and other special purpose machines.
Sand Casting Equipment
Typical sand casting manufacturing process starts from making a sand mould which is negative of the part to be casted. To have hollow cavities in the cast part, cores must be used. The mould and core are fitted together and the molten metal is poured into it. The core is removed after the metal solidifies by vibration.
Based on their experience in the field for 18 years they offer solutions for Moulding machines, Core shooters, Core sand mixers, Pneumatic conveyors for sand casting process.
Aluminium casting equipment
Aluminum is casted with metal dies. To produce high qualtiy Aluminiun casts, the hydrogen from the moulten metal has to be removed. Hydrogen dissolves when the metal comes in contact with water vapour in air. Hydrogen is removed in the molten metal by purging with nitrogen gas. This reduces porosity in cast and improves mechanical properties of the casted alumium. Hydrogen is degassed using mobile degassing machines in ladle or directly in the furnace
Their Alumium casting equipment porfolio includes Nitrogen degassing, Gravity die casting and porosity tesing machines.
Surface Blasting Equipment
Surface blasting machines (sand blasting equipment / shot blasting equipment) are used to clean, peen, polish or improve surface texture. The components are blasted by shots/sand under pneumatic pressure by strategically located nozzles. They are done in enclosed or open space. Usual blasting mediums include metal beads, sand particles, glass beads, etc.
Shot blasting Machines
- Hanger type shot blasting machine
- Drum type shot blasting machine
- Conveyor type shot blasting machine
Sand Blasting Machine
SBE Series Sand Blasting Machinery
Delicate and Precise Finishes Suction Feed:
Suction fed cabinets are generally selected for light – to medium production requirements and limited space. A Suction feed system uses a venturi siphoning action to draw the media into the compressed air stream within the gun nozzle itself. One pass of the nozzle removes foreign matter in seconds and quickly produces a clean uniform surface finish. The use of a media cyclone separator is optional with suction feed systems.
Controlled Power Pressure Feed:
SBE 14 | SBE 10 | SBE 8 | SBE 6 | |
Internal Blast Chamber Dimensions (WxDxH) mm | 1400x1000x1100 | 100x540x715 | 800x500x600 | 600x500x500 |
Cabinet Overall Height (mm) | 2400 | 1700 | 1600 | 1500 |
Side Door(WxH) mm | 1000×1000 | 800×600 | 600×600 | 500×500 |
Front/Top Door (WxH) mm | – | 500×600 | 500×500 | 500×400 |
Dust Collector | optional | standard | standard | standard |
Motor Power | 2.2 KW | 1.5 KW | 0.75 KW | 0.75 KW |
Air Flow | 11 m³/min | 11 m³/min | 11 m³/min | 7 m³/min |
Filter Air | 9.3 m² | 3.2 m² | 1.8 m² | 1.8 m² |
Filter type | Fabric | Fabric | Fabric | Fabric |
Filter Clamping System | Manual Shake/ Pulse Air | Manual Shake/ Pulse Air | Manual Shake | Manual Shake |
Designed for speed, giving faster cleaning times (up to four times faster than venture system) to meet higher production requirements, pressure feed cabinets are excellent for removing tough hard scale deposits particularly within hard-to-reach recessed areas and complex shapes.
The use of pressure vessel forces a flow of media to the blast nozzle at high impact velocities this is particularly important where dense metallic grits are used to impart deep etching prior to bonding or coating.
SB Protable Series Sand Blasting Machinery
Application :
- Descaling, deburring and deflashing of forged and die casting components
- Steel fabrication can be descaled after welding or derusted, ready for painting
- Quite usefull for overhauling, general maintance and repair work iin cement, chemical and gas plants
- Blast cleaning to remove scale, corrosion rust and paint from deck, hulls, super structure etc.
SB 50 | SB 100 | SB 200 | SB 400 | |
Abrasive Capacity Sand (Kg) | 60 | 100 | 200 | 400 |
Overall Dimensions | ||||
Height (mm) | 1110 | 1290 | 1370 | 1610 |
Diamter(mm) | 360 | 460 | 615 | 615 |
Blast Nozzle (mm) (tungsten carbide lined orifice) | 6 | 6 | 8 | 8 |
Approx Cleaning rate (m²/hr) | 3-4 | 5-9 | 11-15 | 15-19 |
Compress air requirements m³/min(cfm) [at 5.65/cm²(psi)] | 1.25(45) | 2.41(85) | 3.85(135) | 7.08(250) |
Requirement Abrasive size range BS Mesh | 30-80 | 30-80 | 30-80 | 30-80 |
Investment casting equipment
Also called as lost wax process, is a method to produce complex and fine shape under low costs. A mould of the final shape is casted in wax. Then it is coated with ceramic and dried. The wax is then removed from the ceramic in an autoclave by stream under high pressure.
Their Investment casting equipment portfolio includes Autoclave and Wax injection machine.
Band Saw
They manufacture vertical band saw for metal cutting used for alumium profiles and wood working process.
G.S.Machineries
SF No:299, Oraikalpalayam Pirivu,
Kunnathur, Annur (TK),
Coimbatore – 641107.
Tamil Nadu, India
+91-9042043027, +91-9042083752
gsmachineries@gmail.com
gsmachineries.info@gmail.com
You may also be interested in this abrasives machinery manufacturer:

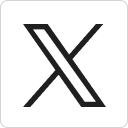




One thought on “G.S.Machineries”