Sree Sakthi Equipments specialize in integrated foundry molding sand plants and the manufacture of foundry equipment and machinery.
The company has been certified as an ISO 9001 company by DNV (Det Norske Veritas – Netherlands) for its quality management system standard.
They have commissioned several low cost, high yield foundries on turn key basis in India and abroad.
The company’s product range includes:
- Foundry Molding Sand Plant Type 1
- Foundry Molding Sand Plant Type 2
- Shot Blasting Machine
- Moulding Machine
- Knockout Cum Feeder
- Punch Out Machine
- Box Closing Machine
- Line Aerator
- Lump Breaker
- Sand Cooler
- Intensive Mixer
- Sand Mix Mullar
- Core Sand Mixer
- Polygonal Sieve
- Ladle
- Ladle Pre-Header
- Sand Drier
- Pedestal Grinder
- Swing Frame Grinder
- Vibratory Feeder
- Mould Box
- Mould Accessories
- Bucket Charger
- Vibratory Shakeout
- Dust Collector
- Apron Conveyor
- Overhead Conveyor
- Wedge Cutter
- Tumblast Machine
- Reclamation Plant
- Compaction Table
- Pneumatic Conveyor
- Cold Box Core Shooter
- Bucket Elevator
- Belt Conveyor
TYPICAL FOUNDRY MOLDING SAND PLANT – TYPE 1
SAND PREPARATION SECTION
Sand preparation plants are available in all sizes to suit modern engineering practices. Sand preparation plants provide uniform and high-quality molding sand. Sand plants are designed to suit customer requirements, actual building conditions and environmental requirements.
SAND PREPARATION PLANTS COMPRISING OF:
- Belt conveyors
- Bucket elevators
- Polygonal sieve
- Sand cooler
- Sand storage hoppers
- Load cell systems,
- Intensive sand mixers
- Moisture controller
- Sand aerators,
- Lump breakers & etc.
SPECIAL FEATURES
- Cost effective
- Consistency in sand quality
- Reduction in man power
- Preparation of high-quality molding sand
- Can be designed to customer requirements
TYPICAL FOUNDRY MOLDING SAND PLANT – TYPE 2
SAND PREPARATION SECTION
The Sand preparation is one of the important activities in the Foundry. In this, the sand is prepared for the manufacture of the Mould. The return sand from the return sand hopper is discharged through a uniform arrangement fed into the feeder belt conveyor for charging the sand into the two-way chute. The New Sand from the hopper is conveyed to the Intensive Mixer through the two-way chute by a vibro feeder kept below the new sand hopper discharge portion.
The Additives like Bentonite and Coal dust are stored in the additive hoppers and there will be a screw conveyor below the additive hopper to discharge the sand to the Feeder Belt Conveyor from the Feeder Belt Conveyor the materials are conveyed to the Two-way chute.
After receiving the return sand, new sand and additives as a batch through Two-way chute, the batch hopper will deliver the sand into the mixer shell. At the time of mixing the water will be automatically added into the shell and the mixing will be made uniform. After completion of the mixing process, the sand is delivered and fall into the surge hopper. From Surge hopper, the prepared sand is conveyed to the Moulding sand hoppers kept above the Moulding machines through the distribution belt conveyor.
The surge hopper allows only uniform controlled sand to travel on the distribution belt conveyor. At distribution belt conveyor, Straight ploughs are placed for diverting the prepared sand into the Moulding Sand hopper.
MOULDING SECTION
The sand from the Distribution Belt Conveyor is received by the Moulding Sand Hoppers. At bottom of the Moulding sand hopper, the fish mouth gate or belt conveyor is fixed. By this fish mouth gate or belt conveyor arrangement, the amount of required prepared sand can be taken by opening the door and the door can be closed (Elec. On/off). Then the sand will fall on the moulding boxes kept above the Moulding Machine table, for preparation of the Moulds. The spilled sand from the Moulding Machine is collected by the Grid with chute provided at the bottom of the moulding machine and it is conveyed through the Spillage belt conveyor to the knockout belt conveyor. The Grid with chute is provided below the end chute to receive the unwanted, rejected mix from the belt conveyor and travel along the spillage belt conveyor for recycling purpose.
MOULD HANDLING SYSTEMS
The Moulds are prepared with the help of the Moulding Machine. The Prepared Moulds are first lifted with the electrical hoist fitted on a trolley of the Bi-rail arrangement. The provision is provided in the Moulding boxes for easy handling through a electric hoist and tackles. The lifted moulds are kept on the trolley which is moving over the closing machine.
After closing, the closing clamps are fitted to ensure that there is no lift of mould during pouring of liquid metal. After pouring again with the help of the transfer trolley provided at the knockout side the moulds are transferred to the knockout / return line and the empty boxes after knockout are moved to the moudling area through this track. In the moulding area, the top box is first taken by the first and cope machine and then the drag box by second machine using the bi-rail arrangement and the electric hoist. The empty pallet car is transferred through a transfer trolley to the mould closing line with the help of mould transfer track provided on the back of the moulding machine.
For Clamping and closing of the Top and Bottom boxes a special clamp and pins are used, the clamp is made in such a way that the boxes are prevented from lifting and pouring of the Molten Metal.
POURING SYSTEM
The Ladles will be hanged in the Monorail pouring beams through ladle handlers, which makes the ladle to move up and down on the vertical direction and the monorail trolley fixed on the Monorail beam ensures the horizontal/longitudinal movement on the ladle. Also, the ladles are provided with gear box mechanism, which makes the ladle to tilt towards the mould and pour the metal into the moulds.
With the arrangement, a single person is sufficient to pour the Moulds easily. Before charging the Molten Metal in the ladle, the ladle has to be preheated. After Charging the molten metal at will be transfer to pour the mould.
FOUNDRY EQUIPMENT FOR SAND HANDLING
The Mould/Casting and the sand is separated with the help of Knockout system. In this knockout it is provided with structure and a monorail arrangement. In this and electric hoist is fixed on a trolley which moves on the monorail system. With the help of the electric hoist and the monorail system, the boxes are taken form the mould car and kept on the knockout machine, due to the vibration of the mould and sand are gets separated and the sand is collected from the bottom through a chute which directs the sand to the vibratory feeder and the casting will be taken out from the top of the knockout. After knockout the boxes are brought back to the track and kept with the help of the same electric hoist. The arrangement is in such a way that even during knockout the mould boxes are not detached from the electric hoist tackle.
The collected sand under the knockout is continuously conveyed through the vibrating feeder and discharged into the Belt Conveyor. During conveying itself the metal particles like fines and small iron pieces are taken out by the over band magnetic separator fitted above and across the belt conveyor. The discharged sand from the belt conveyor is charged into the bucket elevator and the bucket elevator discharges the sand into the polygonal sieve, where the sand is sieved to remove the core, lumps and any other bigger particle. The sieved sand is collected in the sand hopper fitted below the polygonal sieve and the discarded lambs are discharged through a separate chute.
The sand hopper below polygonal sieve is also fitted with a screw feeder mechanism which ensure the uniflow feeding of sand to the sand cooler. The cooling of sand is very essential since the knocked-out sand will be very hot of about 160 to 180 C. which is to be cooled to about 45 C to 50 C suitable for the sand preparation. The sand cooler also does the function of removing the fines and dust available on the sand which spoils the sand property.
The cooled sand is stored in the storage bunker through a bucket elevator provided. The storage hopper is provided with a uniflow attachment which ensure that uniform quantity of sand is allowed at any point of line under the storage hopper.
FOUNDRY EQUIPMENT: SAND MOULDING MACHINE
- Free floating anvil for shockless jolting to protect your foundation.
- Precisely guided pin lift with Hydro-pneumatics.
- Hydro – Pneumatic swing in – swing out.
- Centralised Forced lubrication on every cycle to ensure longer life of wearing parts.
- Simple pneumatic controls for easy maintenance.
- Hand wheel operated squeeze plate adjustment.
- Short cycle time due to low amplitude, high frequency jolting mechanism to meet stringent conditions of automised moulding line.
FOUNDRY EQUIPMENT: LUMP BREAKER
Salient Features
- Lump breaker are simple robust and dependable to Modern Engineering Practise.
- Specially designed for continuous duty for breaking the lumps present in the return sand
- Breaking takes place by high-speed rotors.
- The Rotors blades are lined with high wear resistant material.
- The inner side of Lump breakers are lined with high wear resistant material.
- Lumps are thrown against the chains fixed on the opposite side of the rotors.
- Ranges offered:6 Tons/Hr to 100 Tons/Hr.
FOUNDRY EQUIPMENT: CORE SAND MIXER
Salient Features
- SSEC Heavy duty sand Millers are of study constructions and easy to maintain.
- The adaptation of a successful procedure to modern requirements of sand
- preparation at increased rotary
- Speed and adjustable pressure.
- The possibility of adjustment of the Muller pressure creates the best conditions
- for all types of sand.
FOUNDRY EQUIPMENT: SAND COOLER
RETURN SAND IN GREEN SAND FOUNDRY
Return Sand Temperature, after the vibratory shake out in a mechanized green sand foundry is around ZOOGC. The sand temperature is highest adjacent to the metal surface and lowest away job it. The quantity of heat to be removed depends on the sand to metal ratio and the holding time of metal in the mould. The return sand temperature at the inlet of the cooled after passing through conveyor is around 1 OOOC. Mould of good quality and clean casting surface require well cooled sand.
Sand Cooling requires a continuous and uniform flow to achieve the uniform flow and compensate for irregular Sand supply the sieved hot return sand is stored in a surge hopper from there; a belt transports the hot sand to the cooling conveyor which is designed with a perforated bottom plate. Fresh air is blown through the preparation holes and at the same time water is sprayed on to the sand from nozzles located above the conveyor vibrations of the conveyor and turbulence caused by the air blown through ensure that sand water mix well so that The water evaporates and the sand is cooled. The belt, the cooling conveyor and the sand spraying unit are controlled by level indicators located in the surge hopper the plant operates only if the sand in the surge hopper is between the maximum and minimum level.
FOUNDRY EQUIPMENT: SAND MIX MULLAR
Salient Features
- SSEC Heavy duty sand Mixer / Muller are of sturdy construction and easy to maintain.
- The adaptation of a successful procedure to modern requirement of sand preparation
- at increased rotary speed and adjustable pressure.
- The possibility of adjustment of the Muller pressure creates the best conditions for all
- types of sand.
- Muller pan is protected with wear resisting replaceable bottom plates and the sidewalls
- within the zone of the scrapers.
- Two scrapers are so designed that one brings the sand under the Muller and the other takes it out.
- The scrapers are brazed with tungsten carbide tips.
- Crib is fabricated from MS Plates are reinforced at the top and bottom to prevent any disturbance while the machine is working.
- The crib is bolted to the pan base and is detachable for maintenance purpose.
- Best quality and tested raw materials are used and hence long life is ensured even at high working rate.
- Special housing assembly ensures no leakage of sand and water from the pan.
Sree Sakthi Equipments Company,
Manufacturer of Foundry Equipment
898/2, Bettathapuram,
Karamadai Post,
Coimbatore – 641 104.
Phone No: 04254-272165, 273135.
sales@sreesakthiindia.com
cbe@sreesakthiindia.com
https://sreesakthiindia.com/index.html
You may also be interested in this manufacturer:

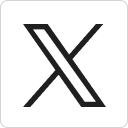




One thought on “Sree Sakthi Equipments”