Established in the year 1983, Om Sakthi Industries (OSI) have decades of expertise in providing the best of auto components manufacturing & machining services to a variety of clients who are world’s leading OEM, tier- one auto suppliers. They also cater to Agricultural vehicle manufacturers, Earth movers and other specific industrial needs.
Their core Capabilities:
PROCESS ENGINEERING
OSI is stocked with immense knowledge in designing the processes by adopting the culture of continuous learning and developing designing skills practiced for years which has enabled us to significantly mitigate process designing lead time for product development. We utilize designing software to develop tools which help to program machine and to design flow of process as per the product specification. We have a tool room where we apply the prototype concepts with our toolmakers, welders, and machinists who are more than to help in development and pre-production testing. Each and every process has been designed and followed by set of experts who undertakes the management responsibilities mapping process from pre-production to delivery of products. We have built a status of reliability from customers recognizing us as valuable source for adaptive engineering.
AUTO COMPONENTS MANUFACTURING AND MACHINING
Manufacturing auto components and other industrial products from concept to fully finished components as per customer design and requirement is their core competency. They are equipped with range of multi spindle machineries which helps to manufacture products on large volume with reduced lead time and precise quality viz. auto components that mainly feature in air brakes, hydraulic brakes, Engine systems and transmission systems.
MACHINING
OSI has state of art modern CNC controlled multi axis machineries with different capabilities utilized to machine complex, close tolerance automobile components to provide their customers products as per their requirements. The combination of machining processes includes turning, milling, grinding, drilling, threading and many other conventional machining methods. The applications of these processes are largely utilized to machine OEM, auto parts, agri vehicle parts and earth mover parts. The production flow includes machineries allocated for separate processes on a sequential manner to have control on lean.
ELECTRO PLATING
Electro plating is a unique coating process carried on manufactured auto components and other industrial products to make it corrosion free and a durable product. It is necessary to have coatings on vehicle parts. We have a well-equipped automated eco-friendly electroplating facility with a capacity of 8 metric ton per day. The types of facilities we have for electroplating are
Auto Barrel
Auto barrel is a state-of-the-art zinc plating process in which the coating materials are immersed into a barrel which contains liquid zinc. The metal is rotated and rinsed inside the barrel which provides a perfect coating to the surface from all directions.
Auto Rack
Auto rack plating is a different process compared to that of auto barrel. Auto rack concept works on products which cannot be followed on auto barrel method. Auto rack is specifically designed for specific kind products which are coated under automated hanging racks which is created for the purpose of safe handling and precision coating. The services we offer include.
Zinc Plating
The application of zinc ore onto desired surfaces is called as zinc plating which is one of our core electroplating services. Before the products are coated, they are cleansed by different acids at different temperature which makes the zinc plating finer and making the product durable.
Zinc & Iron Plating
Zinc & iron is a fusion coating which is a non-cyanide alkaline process depositing iron content on zinc layer with which products are coated. Our plating services can match the validation standards of minimum 300 hours and maximum of 400 hours.
Anodizing
Zinc & iron is a fusion coating which is a non-cyanide alkaline process depositing iron content on zinc layer with which products are coated. Our plating services can match the validation standards of minimum 300 hours and maximum of 400 hours.
Chromating
The major application of chromating is to provide a corrosion free surface on metals and alloys which reasonably increases the life of metals. It also protects it from oxidizing which is a major contributor for corrosion.
Phosphating
The point of application of phosphate is to cover the steel surface with an iron phosphate coating. It provides corrosion resistance and durability. The major application of this process is on heavy equipment products.
Blackening
It is the application of ferrous or black oxide coating on steel and other metals and making it corrosive resistant.
SPECIAL PROCESSES:
OSI is also known for its expertise in handling special processes. Our strength is in providing pool of different special process services which helps our customer in getting their job done in one place with desired quality and specifications. We take care of the following processes.
Metal Joining
The combination of two ore more metals of same or different property for application-oriented purposes is important. We focus largely on the strength, durability and practical applications of all products thereby keeping the weight of material at minimal norms.
Pressing
The process of compressing, forming, or deforming a metal to make it usable for a particular application is regarded as pressing. It involves usage of a variety of process and design-based requirement. We have some of the state-of-the-art machines to provide accurate results in perfect tolerances.
Induction Hardening
The surface hardening of steel and various other alloys is called as Induction Hardening.
It constitutes large amount of temperature-oriented control factor to obtain optimum results from the alloy. We do induction hardening process only based on customer request and requirements.
Through Hardening
The method involved in increasing the strength and tensile property of a metal is regarded as through hardening. It is very important for certain products to improve their through hardening in order to improve their wear and tear lifetime.
INSPECTION AND TESTING FACILITIES
It is a key element to know the perfection of a manufactured system and inspection becomes a real important factor. Our inspection equipment are calibrated to comply with ISO 17025 standards and for quality system we comply with ISO 9001:2015(TS16949) standards. We assure quality by following the visual standards with the help of advanced inspection equipment and trained employees. We have inspection stations approved by customers to maintain quality consistency as per customer requirements. We also utilize customized testing machines to test the products that match the validation standards.
Inspection Facilities
1.CMM
2.Contracer
3.Surface Finish Tester
4.Standards Room
5.Profile Projector
Om Sakthi Industries Auto components manufacturing and machining
No : 227/1, Nageswara rao road,
Athipet, Chennai,
Tamilnadu – 600058, INDIA
info@omsakthiindustries.co.in
+91 – 044 – 26880694
+91 – 044 – 26880640
www.omsakthiindustries.in/about-us/
You may also be interested in this auto component manufacturer:

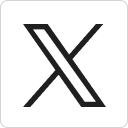



