Adulon Polymers, established in 1997 as a Teflon coating company in Coimbatore, India, focuses on enhancing the performance capabilities of its customers’ products via HVOF Chromium Carbide Coatings. The company holds approved licenses for Teflon, Xylan, Halar, and Peek coatings.
Adulon Polymers maintains an in-house laboratory to develop specialized materials and application methods necessary for new products requiring high-quality coatings. Their in-house capability to design and manufacture equipment and processes strengthens their engineering approach to precision coating applications.
Adulon’s coating processes add value to automotive parts, medical devices, consumer goods, and various other products by creating functional surfaces that solve numerous issues. Problems such as friction, sticking, corrosion, noise, abrasion, and FDA compliance are effectively addressed by Adulon’s expert engineers and innovative coating techniques.
Teflon Coating
Teflon coating, a hallmark of industrial excellence, is offered by DuPont in both powder and liquid forms. Renowned for its unparalleled versatility, these coatings are engineered to address the most challenging non-stick applications while delivering exceptional performance across a spectrum of properties.
Trademarked by DuPont, Teflon is licensed for use by Adulon Polymers, Ltd., ensuring adherence to rigorous quality standards. Teflon coatings encompass seven distinct types, each tailored to specific requirements:
- Teflon PTFE: These coatings, based on Poly Tetra Fluoro Ethylene, comprise two-coat, primer, or top coat systems, boasting the highest operating temperature among all fluoropolymers.
- Teflon FEP: Fluorinated Ethylene Propylene Copolymer coatings, characterized by their ability to melt and flow during baking, form non-porous films with exceptional smoothness.
- Teflon PFA: Similar to FEP, Per Fluoro Alkoxy coatings also melt and flow during baking, offering advantages such as higher continuous use temperature, increased film thickness, and greater toughness compared to PTFE or FEP.
- Teflon ETFE: Known as Tefzel, ETFE coatings are co-polymers of Ethylene and Tetra-Fluoro ethylene, providing unique performance characteristics.
- Teflon-one coat: These solvent-based liquid coatings blend fluoropolymers with high-performance resins to enhance toughness and abrasion resistance, retaining key properties such as low friction and non-stick characteristics.
- Teflon-S Dry Lubricant: Specially formulated to provide lubrication under high-pressure and high-velocity conditions, Teflon-S Dry Lubricant coatings offer superior performance in demanding applications.
- Teflon SF: The latest addition to the Teflon family, soluble fluoropolymer coatings, dissolved in special per fluorocarbon solvents, are designed for thin-film applications ranging from less than 1 micron to 5 microns.
These coatings exhibit a myriad of outstanding properties, including:
- Non-stick attributes, ensuring easy release of substances and minimizing adhesion.
- Low coefficient of friction, facilitating smooth movement and reducing wear and tear.
- Non-wetting properties, repelling liquids and preventing absorption.
- Heat resistance, maintaining integrity under high-temperature conditions.
- Unique electrical properties, making them suitable for specialized applications.
- Cryogenic stability, retaining performance even at extremely low temperatures.
- Chemical resistance, safeguarding against corrosion and degradation in harsh environments.
In summary, Teflon coatings represent a pinnacle of engineering excellence, offering unparalleled performance and versatility across diverse industrial applications.
Halar Coating
Halar coating, also known as ECTFE, boasts a proven track record across a broad spectrum of chemical processing applications, where it serves as a highly sought-after solution for safeguarding critical components. Widely deployed as a protective coating for exhaust ducts, vessels, and various process equipment, its versatility and reliability have made it indispensable in numerous industrial settings.
One of the standout features of Halar coatings is their exceptionally smooth surface, which plays a pivotal role in mitigating the risk of pinholes in the coating. This smoothness not only enhances the aesthetics but also inhibits the buildup and accumulation of particles on the coated surface. This attribute is particularly advantageous in environments where cleanliness is paramount, such as semiconductor exhaust equipment, where even minor particle contamination can have adverse effects on performance.
In addition to its surface properties, Halar exhibits outstanding permeation resistance, making it an ideal choice for applications requiring stringent chemical resistance. It effectively withstands exposure to a wide array of solvents and acids/bases, spanning the entire pH spectrum from 1 to 14. Whether encountering aggressive substances like Hydrofluoric Acid, Sulfuric Acid, Nitric Acid, or corrosive agents like Hydrogen Peroxide, Ozone, and Ammonium Hydroxide, Halar coatings stand resilient, ensuring reliable protection for underlying substrates.
Furthermore, Halar coatings have earned acclaim for their role in corrosion protection within the chemical processing industry (CPI). Their ability to withstand corrosive environments and resist chemical degradation makes them a trusted choice for safeguarding critical infrastructure and equipment, thereby contributing to the longevity and operational integrity of industrial facilities.
In summary, Halar coating stands as a testament to durability, versatility, and reliability, offering a comprehensive solution for protecting surfaces against corrosion, chemical exposure, and particle contamination in diverse industrial applications.
Peek Coating HVOF Chromium Carbide Coatings
Peek polymer stands as a pinnacle among high-performance materials globally, esteemed for its exceptional attributes. Catering to a multitude of industries, Peek polymer’s standard or general-purpose product range addresses diverse customer needs with precision. This comprehensive product line offers a distinctive fusion of properties, blending mechanical robustness with high-temperature resilience to elevate part functionality, ensure long-term reliability, and foster cost-effectiveness for clientele.
The benefits of Peek coating are manifold:
Firstly, it exhibits remarkable strength, stiffness, and dimensional stability even in the most challenging high-temperature and harsh environmental conditions. This inherent robustness enables Peek-coated components to withstand rigorous operational demands without compromising performance.
Secondly, Peek’s lightweight nature and ease of processing present distinct advantages over conventional materials like steel, aluminum, and titanium. Its facile processing capabilities streamline manufacturing processes while reducing overall weight, thereby enhancing efficiency and resource utilization.
Furthermore, Peek coating boasts a low coefficient of friction coupled with high wear resistance, eliminating the need for lubrication in applications prone to frictional wear. This feature not only reduces maintenance requirements but also extends the operational lifespan of coated components, resulting in tangible cost savings for end-users.
Moreover, Peek exhibits exceptional chemical resistance, remaining insoluble in commonly encountered solvents such as acids, salts, and oils. This resistance to chemical degradation ensures the integrity of coated parts even in corrosive environments, enhancing their durability and longevity.
Additionally, Peek coating features low outgassing and minimal particle generation, underscoring its intrinsic purity and suitability for applications where contamination control is paramount. By minimizing the risk of contamination, Peek-coated components contribute to the reliability and performance consistency of critical systems.
In essence, Peek coating emerges as a versatile and reliable solution, offering a harmonious blend of mechanical strength, thermal stability, chemical resistance, and purity. Its myriad benefits empower industries across sectors to optimize performance, enhance reliability, and achieve sustainable cost efficiencies in their operations.
Xylan Coating HVOF Chromium Carbide Coatings
Xylan stands as the preeminent and most comprehensive line of fluoropolymer coatings worldwide, renowned for its diverse array of properties tailored to suit an extensive range of applications. Its versatility renders it suitable for an infinite variety of uses, making it a staple choice across industries.
Distinguished by its composition, Xylan coatings represent a departure from conventional fluoropolymer coatings. They are composite materials that amalgamate lubricants with unparalleled coefficients of friction alongside state-of-the-art high-temperature-resistant organic polymers. This unique combination results in the formation of “plastic alloys” endowed with distinctive properties.
Key characteristics of Xylan coatings include:
- Low Coefficient of Friction: Achieving remarkably low coefficients of friction, some as minimal as 0.02, Xylan coatings facilitate smooth and efficient operation across various applications.
- Superb Wear Resistance: Even under extreme pressures, Xylan coatings demonstrate exceptional wear resistance, ensuring prolonged durability and reliability.
- Outstanding Corrosion and Chemical Resistance: In diverse environments, Xylan coatings exhibit remarkable resilience against corrosion and chemical degradation, enhancing the longevity of coated surfaces.
- Flexible Curing Schedule: With a curing range spanning from ambient temperatures to as high as 425°C (8000°F), Xylan coatings offer flexibility in application and adaptability to varying operational conditions.
- Wide Colour Range: Xylan coatings are available in a broad spectrum of colors, facilitating color-coding for product differentiation and identification purposes.
- Pliability: Xylan coatings possess a remarkable degree of pliability, allowing them to bend freely and repeatedly without risk of breaking, ensuring durability in dynamic applications.
- Machineability: Most formulations of Xylan coatings support the application of multiple coats and machining processes, offering versatility in manufacturing and customization.
- Excellent Adhesion: Xylan coatings exhibit strong adhesion to a wide range of substrates, including metals, plastics, ceramics, wood, and even themselves, ensuring robust bonding and long-lasting performance.
In summary, Xylan coatings represent a pinnacle of coating technology, offering a comprehensive solution for enhancing surface properties, extending component lifespan, and improving operational efficiency across diverse industries and applications. HVOF Chromium Carbide Coatings
High-Velocity Oxy-Fuel (HVOF) Coating
High-Velocity Oxy-Fuel (HVOF) coating is a thermal spray coating process used to improve or restore a component’s surface properties or dimensions. Here are some common types of HVOF coatings:
- Tungsten Carbide Coatings
- Tungsten Carbide-Cobalt (WC-Co): Known for its excellent wear resistance and hardness, used in high-stress applications.
- Tungsten Carbide-Cobalt-Chromium (WC-Co-Cr): Offers superior corrosion resistance along with wear resistance, ideal for harsh environments.
- Chromium Carbide Coatings
- Chromium Carbide-Nickel Chromium (Cr3C2-NiCr): Provides excellent wear and corrosion resistance at high temperatures, suitable for aerospace and industrial applications.
- Metal Alloy Coatings
- Stellite: A cobalt-based alloy with high hardness and resistance to wear, corrosion, and high temperatures, commonly used in valves and turbine blades.
- Inconel: A nickel-chromium alloy that provides excellent oxidation and corrosion resistance at high temperatures, used in aerospace and chemical processing industries.
- Ceramic Coatings
- Alumina (Al2O3): Offers excellent electrical insulation, high hardness, and wear resistance, used in electrical and electronic applications.
- Zirconia (ZrO2): Provides high temperature and thermal barrier properties, commonly used in thermal barrier coatings for gas turbine engines.
- Cermet Coatings
- Nickel-Aluminum (NiAl): A combination of metal and ceramic materials that provides a balance of toughness and wear resistance, used in various industrial applications.
HVOF coatings are applied using a process that combines fuel (such as hydrogen or kerosene) and oxygen in a high-pressure combustion chamber, producing a high-velocity stream of heated particles. These particles are then sprayed onto the substrate, creating a dense and well-adhered coating with superior mechanical properties.
ADULON POLYMERS HVOF Chromium Carbide Coatings
116-B, Athipalayam Road,
Chinnavedampatti,
Ganapathy, Coimbaotre – 641 006.
Phone: 0422 – 2668422
Mobile: 93444-27595
Email: adulon@in.com | info@adulon.in | nandakumar@adulon.in
https://www.adulon.in/index.html
You may also be interested in this company offering HVOF Tungsten Carbide Coating services:

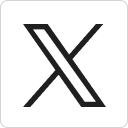




One thought on “Adulon Polymers”