Established in 2000, Shafel Tech is a leading provider of high-quality HVOF Tungsten Carbide Coating and other thermal spray coatings. The company caters to a range of industries, offering a range of precision carbide, ceramic, and metal coatings using advanced surface coating technologies such as detonation spray coating (DSC) and robot-mounted high velocity oxy-fuel (HVOF) coating. Shafel Tech is known for its expertise in applying coatings with excellent adhesion, toughness, and wear resistance, making it a trusted partner for companies seeking high-performance coatings. Whether you need coatings for aerospace, automotive, or energy applications, Shafel Tech has the experience and capabilities to deliver reliable and effective solutions.
HVOF Tungsten Carbide Coating
High velocity oxy-fuel (HVOF) tungsten carbide coatings are coatings that are applied using the HVOF thermal spray process and consist of tungsten carbide particles suspended in a bonding matrix. Tungsten carbide is a hard and abrasive material that is known for its excellent wear resistance, making it an ideal choice for applications that require high levels of wear protection.
HVOF tungsten carbide coating is typically applied to surfaces that are subjected to high levels of wear and abrasion, such as machine parts, cutting tools, and wear plates. They are often used in industries such as aerospace, automotive, construction, and mining, where components are subjected to extreme operating conditions.
HVOF tungsten carbide coatings can provide a number of benefits, including improved wear resistance, improved corrosion resistance, and improved fatigue resistance. They can also improve the life of components by reducing the need for frequent replacement and maintenance.
However, it is important to note that HVOF tungsten carbide coatings can be difficult to apply and require specialized equipment and trained operators. They are also typically more expensive than other types of coatings, such as hard chrome plating or electroless nickel plating.
Chromium Carbide Coating HVOF Tungsten Carbide Coating
Chromium carbide (CrC) coatings are thin layers of hard, wear-resistant material that are applied to surfaces to improve their resistance to wear and abrasion. CrC coatings are typically composed of chromium carbide particles suspended in a bonding matrix, which can be a metal, ceramic, or polymer material.
CrC coatings are often used to protect surfaces that are subjected to high levels of wear and abrasion, such as machine parts, cutting tools, and wear plates. They are often used in industries such as aerospace, automotive, construction, and mining, where components are subjected to extreme operating conditions.
CrC coatings are known for their excellent wear resistance and are often used as an alternative to hard chrome plating or tungsten carbide coatings. They can provide a number of benefits, including improved wear resistance, improved corrosion resistance, and improved fatigue resistance. They can also improve the life of components by reducing the need for frequent replacement and maintenance.
There are several methods that can be used to apply CrC coatings, including thermal spray techniques such as high velocity oxy-fuel (HVOF) spraying, plasma spraying, and flame spraying, as well as electroplating techniques such as electroless nickel plating. It is important to note that CrC coatings can be difficult to apply and require specialized equipment and trained operators.
Chromium Based Hard Coating in Various Matrix
Chromium is a chemical element with the symbol Cr and atomic number 24. It is a hard, silvery-gray metal that is highly resistant to corrosion and tarnishing, and it has a high melting point and good electrical conductivity. Chromium is commonly used as a hard coating on various materials, including metals, plastics, and ceramics, in order to improve their wear resistance and corrosion resistance.
There are several methods for applying a chromium coating, including electroplating, physical vapor deposition (PVD), and thermal spraying. Electroplating involves using an electrical current to deposit a thin layer of chromium onto the surface of a material. PVD involves vaporizing a chromium compound and depositing it onto the surface of a material using a high-energy beam or plasma. Thermal spraying involves using a high-velocity stream of particles to deposit a layer of chromium onto the surface of a material.
Chromium coatings are often used in a variety of applications, including automotive parts, machine tools, cutting tools, and medical implants. They can also be used in decorative applications, such as in the production of chromium-plated automotive trim and household appliances.
It is important to note that chromium is a toxic element, and appropriate precautions should be taken when working with chromium coatings. In addition, chromium compounds can be harmful if inhaled or ingested, and they may cause skin irritation or allergies.
Nickel Based Hard Coating in Various Matrix
Nickel is a chemical element with the symbol Ni and atomic number 28. It is a silvery-white metal that is highly resistant to corrosion and has good electrical and thermal conductivity. Like chromium, nickel is commonly used as a hard coating on various materials in order to improve their wear resistance and corrosion resistance.
There are several methods for applying a nickel coating, including electroplating, physical vapor deposition (PVD), and thermal spraying. Electroplating involves using an electrical current to deposit a thin layer of nickel onto the surface of a material. PVD involves vaporizing a nickel compound and depositing it onto the surface of a material using a high-energy beam or plasma. Thermal spraying involves using a high-velocity stream of particles to deposit a layer of nickel onto the surface of a material.
Nickel coatings are often used in a variety of applications, including aerospace components, automotive parts, machine tools, and medical implants. They can also be used in decorative applications, such as in the production of nickel-plated jewelry and household appliances.
Like chromium, nickel is a toxic element, and appropriate precautions should be taken when working with nickel coatings. In addition, nickel compounds can be harmful if inhaled or ingested, and they may cause skin irritation or allergies. It is important to follow proper safety protocols when working with nickel and nickel-based coatings.
Alumina – Titania Ceramic Coating
Alumina-titania coatings are thin layers of material that are composed of a mixture of aluminum oxide (alumina) and titanium oxide (titania). These coatings are often used for their excellent wear resistance, corrosion resistance, and high temperature stability.
There are several methods for applying alumina-titania coatings, including physical vapor deposition (PVD), chemical vapor deposition (CVD), and sol-gel techniques. PVD involves vaporizing a mixture of alumina and titania compounds and depositing them onto the surface of a material using a high-energy beam or plasma. CVD involves reacting gaseous precursors to form the coating on the surface of a material. The sol-gel technique involves forming a gel-like solution that contains the desired coating materials, which is then applied to the surface of the material and allowed to dry.
Alumina-titania coatings are often used in a variety of applications, including aerospace components, automotive parts, cutting tools, and medical implants. They can also be used in decorative applications, such as in the production of high-end ceramics and glassware.
It is important to note that both alumina and titania are stable and non-toxic materials. However, as with any coating process, appropriate safety precautions should be taken to protect against inhaling or ingesting the materials, and to prevent skin irritation or allergies.
Alumina (99.7%) Coating HVOF Tungsten Carbide Coating
Alumina, also known as aluminum oxide (Al2O3), is a hard, crystalline material that is highly resistant to wear, corrosion, and high temperatures. It is widely used as a coating material due to its excellent properties.
There are several methods for applying an alumina coating, including physical vapor deposition (PVD), chemical vapor deposition (CVD), and sol-gel techniques. PVD involves vaporizing an alumina compound and depositing it onto the surface of a material using a high-energy beam or plasma. CVD involves reacting gaseous precursors to form the coating on the surface of a material. The sol-gel technique involves forming a gel-like solution that contains the desired coating material, which is then applied to the surface of the material and allowed to dry.
Alumina coatings are often used in a variety of applications, including aerospace components, automotive parts, cutting tools, and medical implants. They can also be used in decorative applications, such as in the production of high-end ceramics and glassware.
It is important to note that alumina is a stable and non-toxic material. However, as with any coating process, appropriate safety precautions should be taken to protect against inhaling or ingesting the material, and to prevent skin irritation or allergies.
Detonation Spray Coating Technology
Detonation spray coating (DSC) is a type of thermal spray technology that involves the formation of a plasma jet by the detonation of a fuel-oxidizer mixture. This plasma jet is then used to melt and vaporize a stream of feedstock material, which is then deposited onto a substrate to form a coating.
DSC is typically used to apply coatings of ceramics, metals, and other materials onto a variety of substrates. The process is known for its high deposition rates and ability to produce coatings with excellent adhesion, toughness, and wear resistance. It is often used in applications that require high-performance coatings, such as those in the aerospace, automotive, and energy industries.
One of the main advantages of DSC is its ability to produce coatings with a high level of purity, as the feedstock material is vaporized in the plasma jet and does not come into contact with the atmosphere until it is deposited onto the substrate. This can be beneficial in applications where the presence of contaminants or impurities in the coating could be detrimental to its performance.
DSC also has a number of other advantages, including the ability to apply coatings to complex geometries, the ability to produce coatings with a wide range of thicknesses, and the ability to apply coatings to materials that are difficult to coat using other methods. However, it is important to note that DSC can be a complex and technically challenging process, and it requires specialized equipment and trained operators.
High Velocity Oxy Fuel Spray System
High velocity oxy-fuel (HVOF) spray is a type of thermal spray technology that involves the use of a high-pressure oxygen fuel gas mixture to propel a stream of feedstock material onto a substrate. The feedstock material is typically in the form of a powder or wire, and it is melted and vaporized by the high-velocity gas stream as it is sprayed onto the substrate.
HVOF spray is often used to apply coatings of metals, ceramics, and other materials onto a variety of substrates, and it is known for producing coatings with excellent adhesion, toughness, and wear resistance. It is often used in applications that require high-performance coatings, such as those in the aerospace, automotive, and energy industries.
One of the main advantages of HVOF spray is its ability to produce coatings with a high level of purity, as the feedstock material is vaporized in the high-velocity gas stream and does not come into contact with the atmosphere until it is deposited onto the substrate. This can be beneficial in applications where the presence of contaminants or impurities in the coating could be detrimental to its performance.
HVOF spray also has a number of other advantages, including the ability to apply coatings to complex geometries, the ability to produce coatings with a wide range of thicknesses, and the ability to apply coatings to materials that are difficult to coat using other methods. However, it is important to note that HVOF spray can be a complex and technically challenging process, and it requires specialized equipment and trained operators.
Wire Flame Spray Process HVOF Tungsten Carbide Coating
Wire flame spray is a type of thermal spray technology that involves the use of a flame to melt and vaporize a feedstock material, which is then sprayed onto a substrate to form a coating. In the wire flame spray process, the feedstock material is in the form of a wire, which is fed through the flame and melted as it is sprayed onto the substrate.
Wire flame spray is often used to apply coatings of metals, ceramics, and other materials onto a variety of substrates, and it is known for producing coatings with good adhesion and wear resistance. It is often used in applications that require relatively thin coatings, such as those in the automotive, aerospace, and energy industries.
One of the main advantages of wire flame spray is its simplicity and low cost, as it does not require specialized equipment or complex processing steps. It is also relatively easy to operate and can be used to apply coatings to a wide range of materials.
However, wire flame spray does have some limitations, including a lower deposition rate compared to other thermal spray methods and the production of coatings with lower purity compared to methods that vaporize the feedstock material in a gas stream. It can also be more challenging to produce coatings with a uniform thickness using wire flame spray.
Plasma Transferred ARC (PTA) Process
Plasma transferred arc (PTA) is a type of thermal spray technology that involves the use of a plasma arc to melt and vaporize a feedstock material, which is then sprayed onto a substrate to form a coating. In the PTA process, a plasma arc is created between a tungsten electrode and the feedstock material, which is typically in the form of a powder or wire. The plasma arc melts and vaporizes the feedstock material, which is then sprayed onto the substrate to form a coating.
PTA is often used to apply coatings of metals, ceramics, and other materials onto a variety of substrates, and it is known for producing coatings with excellent adhesion, toughness, and wear resistance. It is often used in applications that require high-performance coatings, such as those in the aerospace, automotive, and energy industries.
One of the main advantages of PTA is its high deposition rate, which allows it to produce coatings with a relatively high thickness in a short period of time. It is also capable of producing coatings with excellent surface smoothness and a high level of purity, as the feedstock material is vaporized in the plasma arc and does not come into contact with the atmosphere until it is deposited onto the substrate.
PTA also has a number of other advantages, including the ability to apply coatings to complex geometries and the ability to apply coatings to materials that are difficult to coat using other methods. However, it is important to note that PTA can be a complex and technically challenging process, and it requires specialized equipment and trained operators.
Nitriding/Boronizing Process HVOF Tungsten Carbide Coating
Nitriding and boronizing are surface treatment processes that involve the addition of nitrogen or boron to the surface of a metal or alloy to improve its mechanical and corrosion resistance properties. Both processes involve the use of high temperature and pressure to diffuse the nitrogen or boron into the surface of the material, where it forms a hard, wear-resistant layer.
Nitriding is typically used to treat ferrous metals, such as steel and iron, and it is often used to improve the wear and fatigue resistance of machine parts and tools. Nitriding can be performed using various methods, including gas nitriding, plasma nitriding, and ion nitriding.
Boronizing is typically used to treat non-ferrous metals, such as aluminum and titanium, and it is often used to improve the wear resistance and corrosion resistance of machine parts and tools. Boronizing can be performed using various methods, including pack boronizing and vapor boronizing.
Both nitriding and boronizing can produce coatings with excellent surface hardness and wear resistance, and they are often used in applications that require high-performance parts and tools. However, it is important to note that these processes can be technically challenging and require specialized equipment and trained operators.
Shafel Tech
No:1, Sidco Industrial Estate,
Thirumudivakkam Chennai – 600 044.
Tamilnadu, India
+91 93840 50341
+91 95512 99512
info@shafeltech.com
production@shafeltech.com
http://shafeltech.com/index.html
You may also be interested in this company doing gold plating:

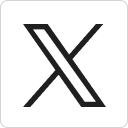



