The EIMCO-K.C.P. Ltd is a Process Technology Company and a leading manufacturer of Liquid – Solid Separation equipment like aerators, diaphragm pump etc for Industrial and Environmental Applications: Thickening, Clarification, Classification, Vacuum Filtration, Aeration Systems etc.
The EIMCO-K.C.P. Ltd was established in 1967 and has more than 25,000 installations worldwide. The EIMCO-K.C.P. Ltd is a wholly owned subsidiary of KCP SUGAR AND INDUSTRIES CORP LTD and is in possession of the EIMCO USA Technology.
The company’s products and technical services are extensively used in Mineral Processing, Chemical Processing, Food Processing, Refining, Pulp and Paper, Power Plant, FGD System, Municipal & Industrial Water and Wastewater Treatment.
Designs are tailored for each application by combining technical data with field, pilots and laboratory test work on the representative slurry sample. Mechanical reliability and ease of maintenance are incorporated into the final product by a design team specializing in product application.
Products
- Swing Lift Thickener
- Thickener
- Clarifiers
- High Rate Solids Contact Clarifier
- Drive Heads
- Clariflocculators
- Spiral Classifier
- High Volume Classifier
- Horizontal Vacuum Belt Filter
- Rotary Vacuum Drum Filters
- Disc Filters
- Dewaxing / Deoiling Filters
- Cane Mud Filters
- Bicarbonate Filters
- Precoat Filter
- Dosing System
- Bar Screen
- Grit Separators
- Aerators
- Mixer / Flocculator
- Causticizing System
- Lime Slacker Classifier
- Rotary Distributor
- Diaphragm Pump
- Reactor Clarifier
- Lamella Clarifier
- Brine Clarifier
Swing Lift Thickener Aerators
EIMCO-K.C.P. Swing Lift thickeners are recommended for high scaling condition and to handle thixotropic solids.
This design uses cables attached to a truss above or near the liquid surface to move the rake arms, which are hinged to the drive structure, allowing the rakes to be raised when excessive torque is encountered.
A major advantage of this design is the relatively small surface area of the raking mechanism, which reduces the solids accumulation and downtime in applications in which scaling or island formation can occur.
Thickener Aerators
High Rate & Conventional types / Hydraulic & Mechanical Drives. Aerators
EIMCO-K.C.P. Thickeners are designed for continuous operation in metallurgical, ore processing, Chemical Industries and also for the water treatment plants. Equipments are designed to accommodate the more sophisticated processes with emphasis on dependable and low cost operation. EIMCO-K.C.P. Thickeners are manufactured for heavy duty Concentrates, tailings and fine application and three basic configurations: Bridge mounted, Column mounted and Traction type and sizes up to 500 feet diameter are available.
Optional lifting devices for either design offer additional operational flexibility.
EIMCO KCP HIGH RATE THICKENERS Aerators
EIMCO-K.C.P. High Rate Thickeners are designed to maximize the flocculation efficiency, self-dilution and settling rates. EIMCO-K.C.P. High rate thickeners are designed to provide high underflow concentration with smaller diameter. The high velocity feed is split to two compartments with opposite tangential inlets that are positioned in two levels, an upper and a lower one. Between those compartments there is a narrow gap through which the flocculent solution is introduced and the high shear quickly distributes the polymer to a uniform mixture.
AUTOMATIC LIFT Aerators
Column Mounted / Bridge Mounted Lifting Device. Hydraulic Lift & Power pack
APPLICATIONS
- Mineral Processing
- Iron
- Copper
- Coal
- Base Metals
- Silver
- Gold
- Platinum group
- Nickel
- Diamond
- Nickel
- Uranium
- Aluminum
- Bauxite
- Mineral Sands
Other Applications
- Grinding
- Concentrate
- Tailing
- Leach
- Clarification
- High Density Slurry
- Counter Current Decantation
- Paste Backfill
- Chemical / Industrial
- Refineries
- Smelters
- Cement Industry
- Gas cleaning plant
- Steel melt shop
- Water Treatment and Waste Water
- Sewage Treatment
- De-salination
- Water purification
THICKENER TANK Aerators
EIMCO KCP Thickener tanks are constructed either from bolted / steel welded or concrete. Most of the chemical process industries prefer the steel tanks construction since they may be elevated above ground level, allow inspection of the tank’s floor for leakages and bring the underflow slurry pumps nearer to the outlet of the discharge cone. Another consideration in selecting steel tanks is their ready adaptation to corrosive processes by rubber covering the wetted parts of the tank.
Clarifiers Aerators
EIMCO-K.C.P.Circular Clarifier are the most common type of sedimentation basin used for separating suspended solids from liquids in the treatment of water, sewage, Industrial waste and industrial process.
EIMCO-KCP designs to majority on special requirements. EIMCO-KCP has installed many one of a kind clarifiers. Experience with thousands of customized unit in operations
EIMCO-K.C.P.Circular Clarifier are the most common type of sedimentation basin used for separating suspended solids from liquids in the treatment of water, sewage, Industrial waste and industrial process.
EIMCO-K.C.P. Offers Bridge mounted (B) type, Column Mounted (C) Type and Traction driven (T) type Classifiers mechanism for various applications. These operate on the common principle of moving settled solids to the center of principle of moving settled solids to the centre of the tank for removal, and differ principally in the method used to support and drive the rotating sludge removal arms.
EIMCO-K.C.P. Classifiers are designed to handle variety of applications & flows and clarifier includes scum skimming device to remove the floating material.
- Primary Clarifiers.
- Secondary Clarifiers.
- Brine Clarifiers for Caustic Soda Industries.
- FGD
- Reactor Clarifiers.
- White Liquid Clarifiers & Green Liquor Clarifiers for Pulp & Paper Industries.
- Lamella Clarifiers.
- High Rate Solids Contact Clarifier
Reactor Clarifier solids contact units allow several different design configurations (varying flocculation distribution, recirculation rates and rake torques) meeting even the most exacting standards for quality.
THE EIMCO-K.C.P. LTD Solids Contact Reactor Clarifiers are basically divided into two different classes HRC and HRB mechanisms.
HRC is the high rate column supported Reactor Clarifier of size ranging from 15m to 75m diameters. HRB is a high rate bridge mounted Reactor Clarifier supplied in sizes ranging from 3m to 25m diameters.
The high rate Solids-Contact Reactor Clarifier operates with the raw influent liquid being brought into immediate contact with a large circulating volume of relatively dense previously formed flocculate and precipitate.
The mixture of raw influent liquid and re circulated slurry is sent upward into the reaction cone with 75-90% being returned to recirculation with the incoming raw water.
The remaining 10-25 % passes under the cone and into the clarification zone. Once in the clarification zone, the solids settle to the tank floor with the clarified liquid moving into the effluent launder and exiting tank
The BFR and CF Reactor Clarifiers are applied to processes where longer detention times within the feed well and no solids recycle are necessary or requested by customer. The detention times are considerably longer than those offered by higher rate solids-contact units and are necessary for proper flocculation.
Drive Heads Aerators
THICKENER / CLARIFIER DRIVE HEADS Aerators
Hydraulic & Mechanical Drives. Aerators
The drive head is the heart of the Thickener & Clarifier mechanism. The present design of The EIMCO-K.C.P. Drive heads is a result of careful study and experience gained over 50 years of operation in the Sedimentation Equipments operating in various Mineral Industries, Chemical Industries, Water Treatment Plants, Sewage and Effluent Treatment Plants under severe operating conditions.
A Sedimentation drive generally operates at a relatively low value of output torque in a well-operated installation. As long as the solids input equals the solids output from the mechanism, torque will begin to climb and the alarm on the drive control will actuate to warm the operator to take corrective action.
Three types of drives are generally used for Clarifier and Thickener Mechanism. “W” Series / “B” Series / “C” Series
The drive head torques up to 4,600,000 ft-lbs.
Hydraulic Drive Heads Aera Aeratorstors
The EIMCO-K.C.P. Hydraulic Drive includes drive unit with bull gear and pinion driven by planetary gear system intern by a hydraulic motor, by a hydraulic power pack. Also the unit includes a torque transducer to activate the overload alarm and to produce an output signal. Automatic rake lifting arrangement and drive tripping arrangement is provided in order to protect the mechanism from overloading.
- The drive is mounted on a lift plate and provided with hydraulic lift arrangement with cylinders.
- Drive Heads with duty rated torque up to 4,600,000 ft-lb’s and peak torque rating up to 13,800,000 ft-lb’s using High Precision Ring Gears are standard on large EKCP Thickeners
- Increased torque capacity.
- Reliable and adjustable torque sensing.
- Hydraulic drive heads are offered for both ‘B’ Type and ‘C’ Type Thickeners.
Mechanical Drive Heads A Aeratorserators
- Spur gear drives, utilized in center column mounted operation, are manufactured with heat-treated cast steel main spur gears, alloy steel pinions, alloy bronze worm gears and hardened steel worms. These are mounted on precision bearings and enclosed by dust tight cast iron housings for oil lubrication. The drives provided with slew ring bearing to withstand high load.
- For bridge-mounted operations, the drive units are manufactured with heat-treated cast steel main spur gears, alloy steel pinions, alloy bronze worm gears and hardened steel worms; all mounted on precision bearings and enclosed by dust tight cast iron housing for lubrication.
- Worm gear drives for smaller units have high quality cast iron main gears with hardened steel worms; mounted on precision ball bearings and enclosed by dust tight cast iron housing for lubrication.
Clariflocculators Aerators
EIMCO-K.C.P. Clariflocculators are combination of both flocculation as well as clarification. With this, the installation of plant becomes economical and faster.
The Clariflocculation is a chemical and physical water treatment process and it mainly consists in the removal of suspended substances. Its application is in the water treatment of surface water, industrial and municipal wastewater treatment, filtration pre-treatment, both in the municipal and industrial sectors.
The Clariflocculation allows the removal of organic compounds, Sedimenting particles and heavy metals.
Peripheral drive clariflocculator with turbine Aerators
The equipment consists of a flocculation zone, inside the cone, a clarification zone, outside the cone, a sedimentation zone at the tank bottom, bottom scrapers to convey the settled sludge to the central drain well, radial ditches to collect the clarified water
The Sedimented sludge flocs are kept in suspension by a turbine, recycled and mixed with the water to be treated. The solids in the incoming water settle over the existing recycled sludge flocs. The new flocs volume increases and they tend to sediment more easily
Peripheral drive clariflocculator with Individual mixers Aerators
The equipment consists of a flocculation zone, inside the cone, a clarification zone, outside the cone, a sedimentation zone at the tank bottom; bottom scrapers to convey the settled sludge to the central drain well, radial ditches to collect the clarified water.
The Sedimented sludge flocs are mixed with the water to be treated by the gate mixers. The solids in the incoming water are mixed with the settled sludge flocs. The new flocs volume increases and they tend to sediment more easily.
Spiral Classifier Aerators
EIMCO-K.C.P. Spiral Classifiers is art of separating the solid particles in a mixture of solids and liquid into fractions according to particle size or density by methods other than screening. In general, the products resulting are (1) a partially drained fraction containing the coarse material (called the underflow) and (2) a fine fraction along with the remaining portion of the liquid medium (called the overflow).
The classifying operation is carried out in a pool of fluid pulp confined in a tank arranged to allow the coarse solids to settle out, whereupon they are removed by gravity, mechanical means, or induced pressure. Solids which do not settle report as overflow.
EIMCO-K.C.P. Spiral Classifiers are mechanically the devices are powerfully built, and functionally they are versatile and flexible.
Today’s worldwide acceptance of EIMCO-K.C.P. Classifiers for washing and dewatering pulps, and in closed-circuit grinding is the result of many years of experience in solving wet classification problems. Because users’ needs vary so greatly, the Classifier is available in a wide range of spiral diameters and pitches, tank shapes and lengths allowing exact compliance with each user’s classification requirements.
Spiral diameters (0.3 m to 2.25 m): Aera Aeratorstors
Important in establishing a correct balance between overflow and raking capacity. Bears directly on accuracy of separation and control of agitation.
Spiral pitches (single / double / triple): Aerators
Number of ribbons is a factor in controlling degree of agitation. Each ribbon of advanced pitch gives greater raking capacity than equivalent ribbon of spiral using lesser pitch. Triple ribbon spiral highly advantageous for slow-speed operations requiring close separations and high raking capacities.
Adjustable spiral speeds: Aerators
Recommended speed of operation given in peripheral MPM is an individual consideration for each ore, and is governed by size, shape and gravity of particle, angle of repose of raking load and desired mesh of separation. Peripheral speeds between 6 and 60 meters per minute are available.
Pool depth: Aerators
Choice of pool depth is directly related to effectiveness of pool area. Series 90 units are employed for coarse separations on down to 212 micron (65 mesh); Series 125 units are employed for separations between 300 and 106 micron (48 and 150 mesh); Series 150 units are employed for separations of 150 micron (100 mesh) and finer.
Lifting device: Aerators
Lifting device eliminates necessity of draining tank during shutdowns. Classifier may be quickly put in operation after shutdown with tank fully sanded. Hydraulic-type standard on all units 1.2 m in diameter and larger. Fast action hand wheel-operated screw- type lift standard on 1.05 m and smaller.
Main Features
- Low Initial Cost.
- Low Operating and Maintenance Cost.
- Adjustable Flexible Lifting Device.
- Simple Flexible Lifting Device.
- Sectionalized Steel Flights.
- Replaceable Wearing Shoe
High Volume Classifier
EIMCO-K.C.P. High volume Classifiers for treatment of industrial wastewater are designed to settle and dewater relatively coarse particles from high- volume, low-percent solid streams. They will make a separation of approximately 35 mesh at 5,000 GPM, and hydraulically transfer flow surges up to 10,000 GPM.
The unique construction of EIMCO-K.C.P. Classifiers permits them to handle a greater volume of wastewater than can be accommodated by other waste treatment devices. The Classifier trough is inclined and flared at the lower end to provide a quite settling pool. A Conveying spiral is mounted within the trough to discharge settled materials above the level of the pool level. Removal of large, abrasive materials by the Classifier helps succeeding equipment perform better and last longer.
Design and Construction Features.
- Low initial cost on operation and maintenance.
- Adjustable spiral speeds to meet most production demands.
- Anti-friction upper and lower bearings for longer service life.
- Replacement wearing shoes.
- Motorized, hydraulic spiral lifting devices for easy start-up after accidental or prolonged shutdown where heavy solids build-up may occur.
- Replaceable abrasion-resistant steel tank liner with bolted construction.
- Sectionalized steel flights.
- Tank is fabricated of heavy steel plate, rigidly braced.
- The drive is complete with totally enclosed, oil lubricated, shaft mounted reducer, V-Belt drive and belt guard.
Horizontal Vacuum Belt Filter
The EIMCO-K.C.P. Horizontal Vacuum Belt Filter has most of the operating capability of a bottom pickup vacuum filter… additionally, it has the operating flexibility to meet particular processing requirements some unique and exclusive capabilities – Simplicity of operation, and fluctuations, the ability to handle feed with low and high solids concentrations, and highly effective cake washing for increased product recoveries and profitability.
EIMCO-K.C.P. offers the most reliable and efficient horizontal belt filters in the field. The designed system is applied for the separation of liquids and solids in various fields as listed below.
WIDEST APPLICATIONS IN THE FIELD OF: Aerators
- Coal, Iron ore, Lead, Copper, zinc, Nickel, etc.
- Flue Gas Desulphurization
- FGD washing of gypsum cake
- Pyrite
- Magnetite
- Phosphate Rock
- Chemical Processing
COSTRUCTIONAL FEATURES AND BENEFITS Aerators
- EIMCO-K.C.P. filters are available from 5 sqm to 200 sqm with belt sizes range from 0.2 m wide to 4.2 m wide of belt width. The belts are imported as factory vulcanized (endless) from reputed suppliers from Europe.
- Rigid structural main frames and cross frames with higher load carrying capacity
- German Planetary drive with variable frequency speed drives, offering speed range up to 30 meters per minute.
- Head pulley and tail pulleys with rubber covered, grooved to provide prevention of belt slippage. Shaft ends with suitable material is offered according to the process.
- Standard pulley bearings from reputed makes of SKF / FAG for the pulleys and rollers.
- Belt support deck with air float as standard feature. Optional systems of roller design / slide rails are provided.
- Vacuum pans designed to provide high liquid handling with material suitable to process.
- For maintenance air operated lowering mechanism of pan is provided with ample space for wear belt change.
- In house Manufacturing capability with Assured quality, certified ISO 9001 company.
FEATURES OF EIMCO KCP HBF Aerators
- Higher Filtration rates with minimum moisture content.
- Lower operating and maintenance costs due to efficient & sturdy design.
- Low friction advanced air box mother belt support system, Variants can be offered with slide rails or roller decks support system.
- Controlled belt aligning systems results in maintenance free running for a long time.
- Multi stage washing.
- Longer life of mother belt due to less friction of air box support.
- Drier filter cake output.
- As the length and process time of each belt filter is configured to suit the application for which it are intended, superior results can be achieved.
TESTING & SIZING TO ENSURE THE END RESULT Aerators
EIMCO-K.C.P. with the expertise of more than 45 years of field experience offers accurate, reliable bench scale and pilot test works to make sure predictable behavior of slurry in the field.
Rotary Vacuum Drum Filters Aerators
EIMCO-K.C.P. Continuous vacuum drum filters are designed to handle the broadest range of slurries of any filter. This permit drum filters to be used in a variety of applications.
Vacuum filters allow a more complete separation of solids from liquids than other mechanical dewatering filters. Vacuum filters are not as dependent on specific gravity differentials for the degree of clarity, nor are they subject to upset due to variation in the process.
EIMCO-K.C.P drum filters provide high filtration rates and have excellent washing characteristics. Wide variations are possible in cycle time to ensure optimum cake formation, dewatering and washing on any application flow sheet. EIMCO-K.C.P. drum filters are ideally suited for filtering solids when cake washing is necessary when a uniform deposit of cake on the media is desired, or when the cake is difficult to discharge.
The five basic discharge types are: Aerators
SCRAPER DISCHARGE Aerators
The EIMCO-K.C.P. Scraper discharge RVDF medium is usually caulked into grooves in the drum grid, with cake removal facilitated by a scraper blade just prior to the re-submergence of the drum.
The scraper serves mainly as a deflector to direct the cake, dislodged by an air blowback, into the discharge chute, since actual contact with the medium would cause rapid wear. In some cases the filter medium is held by circumferentially wound wires spaced 50 mm (2 in) apart, and a flexible scraper blade may rest lightly against the wire winding.
Excellent for heavy solids and typical slurries are easy to filter.
BELT DISCHARGE Aerators
image012The EIMCO-K.C.P. Belt discharge RVDF carrying a fabric that is removed, passed over rollers, washed, and returned to the drum. A special aligning device keeps the medium wrinkle-free and in proper line during its travel.
Thin cakes of difficult solids which may be slightly soluble are good applications. When acceptable, a sluice discharge makes cakes as thin as 1.5 to 2 mm (about gin) feasible.
STRING DISCHARGE Aerators
image014The EIMCO-K.C.P. String discharge RVDF system of endless strings or wires spaced about 13 mm (0.5 in) apart pass around the filter drum but are separated tangentially from the drum at the point of cake discharge, lifting the cake off as they leave contact with the drum.
The strings return to the drum surface guided by two rollers, the cake separating from the strings as they pass over the rollers. If it has the required body, a thinner cake (5 mm) than can be handled by drum filters is feasible, allowing more difficult materials to be filtered. This is done at the expense of greater dead area on the drum. Success depends on the ability of the cake to be removed with the strings and must be determined experimentally.
Applications are mainly in the starch and pharmaceutical industries, with some in the metallurgical field.
ROLLER DISCHARGE Aerators
ROLLER-DISCHARGE A roll in close proximity to the drum at the point of cake discharge rotates in the opposite direction at a peripheral speed equal to or slightly faster than that of the drum.
If the cake on the drum is adequately tacky and cohesive for this discharge technique, it adheres to cake on the smaller roll and separates from the drum. A blade or taut wire removes the material from the discharge roll.
This design is especially good for thin, sticky cakes. If necessary, a slight air blow may be provided to help release the cake from the drum. Typical cake thickness is 1 to 10 mm (0.04 to 0.4 in).
PRE COAT DISCHARGE
PRE-COAT-DISCHARGE The Eimco KCP Pre-coat drum filters are coated with a bed of diatomaceous earth or similar material. During cycling a clear filtrate is obtained. When vacuum is applied, the liquid is drawn through the pre-coat material, and solids deposited on the pre-coat surface are removed along with a thin portion of the pre-coat by an advancing scraper blade, as the drum revolves. The blade operates independently of the drive to provide a “precision lathe: movement. Depending on the movement of the blade the drum can operate up to a week without retracting the blade to apply a new pre-coat bed.
Pre-coat filters are recommended when small amounts of solids are to be removed from large volumes of liquids, for clarification or polishing of effluent, or for the filtration of material that produces sticky solids. They provide a high clarity of filtrate when the filtrate is the valuable product and the cake is to be discarded.
Disc Filters
AGIDISC FILTERS
EIMCO-K.C.P. Agidisc Filter is a vertical leaf rotary vacuum filter particularly adapted to filtration of rapid settling solids. It is widely used in dewatering metallurgical slurries of all types, including coal. A horizontal paddle agitator effectively maintains solids in suspension and prevents uneven cake formation. primary application is in the dewatering phase of the flow sheet.
Most advantageous applications are dewatering of solids which are free settling and from into an easily discharged, non blinding cake.
Maximum filtration area is provided at minimum cost and operating space.
Due to its design, utilizing a filtering surface in a vertical plane, washing of the filter cake is very limited. Guided scraper provides for discharge of thin cakes, reduces wear on media. Wide variety of media – stainless steel screens, cloth and synthetic fabrics are available. Filtering areas range from 2 to 300 m2.
Dewaxing / Deoiling Filters
De-waxing Filters are designed to produce wax free oil and oil free wax in the Petroleum Industries, especially in the lube oil plant.
EIMCO-K.C.P. solvent oil Dewaxing and Deoiling filters are designed for the safe, high capacity removal of wax from lubricating oils at low operating temperatures. Totally enclosed and sealed construction, Positive seal of the valve, rigid support construction of the tank, screen support deck construction and spring mounted Teflon scraper which maintains preset position and is not affected by temperature variations are major features. These units can be instrumented and automated for continuous processing.
Cane Mud Filters
EIMCO-K.C.P. Cane Mud Filters are designed to increase the capacity of acne mud filtering station and at all same time, ensure maximum recovery of sucrose by washing. It incorporates a number of design modifications aimed at making cane sugar operations more profitable. The filter valve with streamlined passages and a system to sweep moisture from piping with air, results in the highest operating efficiency.
The streamlined piping arrangement eliminates all sharp turns in piping. Cake washing is accomplished by spray nozzles spaced evenly for minimum wash water consumption. The scraper blade and slurry level can be adjusted to get the best operation. Maintenance advantages include easily removable filter screens and automatic lubrication.
Every detail of the filter design and construction has been engineered to minimize operating cost for processors of cane sugar.
Process:
The removal of insoluble non-sugar impurities from sugarcane juice is an essential part of raw sugar production and this is commonly achieved through juice clarification.
Dirt collected with sugarcane is processed and separated from the juice in the sugar factory by Cane Mud Rotary Vacuum Drum Filters. New technologies over the past decade have enabled performance improvements to be obtained for this key unit operation. Traditional approach has been to use Rotary Vacuum Drum Filters for processing and separating mud and other impurities from juice.
Cane Mud filtration is the last opportunity for the remaining sugar in mill mud to be recovered. The goals of mud filtration are
(i) Recover sugar and return it as part of the filtrate to the process; and
(ii) Maximize mud solids retention, minimizing the amount of mud recycled back into the process. These two goals are achieved by efficient washing with water.
Bicarbonate Filters
Process:
An Improved process designed for dewatering sodium bicarbonate solids formed on the Surface of the Rotary vacuum drum filter which is discarded for rotation in partial submergence in a slurry containing the suspended solids. The process of Discharge of Cake includes the steps of pressing the filter cake against the surface of the filter drum by means of a pressure-applying roll which is driven to rotate, so that its surface velocity exceeds the velocity of the drum surface and, thereafter, discharging the filter cake from the surface of the filter drum.
This process relates to filtration by pressure-differential techniques and, more particularly, to such a filtration process for dewatering compressible materials like sodium-bicarbonate solids.
EIMCO-KCP Horizontal Vacuum Belt Filters for Sodium Bicarbonate Application
EIMCO-KCP have five Decades of process expertise and continuous technology advancement which are the Anchors on this solid-Liquid Separation Equipment along with proven technology.
Eimco-K.C.P. Sodium Bicarbonate Rotary Vacuum Drum Filters and Horizontal Vacuum Belt filters are typical of the specialized fields for which Eimco-K.C.P. can custom design equipment. Rotary Vacuum Drum filter feature the following:
- Special heavy-duty construction throughout.
- Special back-wash feature to prevent blinding of filter media.
- Special wash system to provide uniform wash-water distribution.
- Special streamlined drainage construction with extra-large valve to insure maximum
- removal of wash liquor and low cake moisture.
- Additional cake compression (Rotary Vacuum Drum Filter) in the removal of moisture from cake.
Precoat Filter
ROTARY VACUUM PRECOAT FILTERS
PRE COAT DISCHARGE
The EIMCO-K.C.P. Pre-coat drum filters are coated with a bed of diatomaceous earth or similar material. During cycling a clear filtrate is obtained. When vacuum is applied, the liquid is drawn through the pre-coat material, and solids deposited on the pre-coat surface are removed along with a thin portion of the pre-coat by an advancing scraper blade, as the drum revolves.
The blade operates independently of the drive to provide a “precision lathe: movement. Depending on the movement of the blade the drum can operate up to a week without retracting the blade to apply a new pre-coat bed.
Pre-coat filters are recommended when small amounts of solids are to be removed from large volumes of liquids, for clarification or polishing of effluent, or for the filtration of material that produces sticky solids.
They provide a high clarity of filtrate when the filtrate is the valuable product and the cake is to be discarded.
The following materials are used to form the Precoat bed:
- Diatomaceous Earth (or Diatomite) consisting of siliceous skeletal remains of tiny aquatic unicellular plants.
- Perlite consisting of glassy crushed and heat-expanded rock from volcanic origin.
- Cellulose consisting of fibrous light weight and ash less paper like medium.
- Special ground wood is becoming popular in recent years since it is combustible and reduces the high cost of disposal. There are nowadays manufacturers that grind, wash and classify special timber to permeabilities which can suit a wide range of applications.
The Precoat Filter is similar in appearance to a conventional Drum Filter but its construction is very different:
The scraper blade on conventional drum filters is stationary and serves mainly to deflect the cake while it is back-blown at the point of discharge. The scraper on a Precoat filter, which is also called “Doctor Blade”, moves slowly towards the drum and shaves-off the blinding layer of the contaminants together with a thin layer of the precoating material. This movement exposes continuously a fresh layer of the Precoat surface so that when the drum submerges into the tank it is ready to polish the solution. The blade movement mechanism is equipped with a precision drive having an adjustable advance rate of 2-10 mm/hr. The selected rate is determined by the penetration of fines into the Precoat bed which, in turn, depends on the permeability of the filter aid. Once the entire Precoat is consumed the blade retracts at a fast rate so that the filter is ready for a new precoating cycle.
The cake discharges on conventional drum filters by blow-back hence a section of the main valve’s bridge setting is allocated for this purpose. On Precoat filters the entire drum deck is subjected to vacuum therefore there are two design options:
A conventional valve that is piped, including its blow-back section, to be open to vacuum during polishing. When the Precoat is consumed its blow-back section is turned on to remove the remaining Precoat heel over the doctor blade.
- A valve less design in which there is no bridge setting and the sealing between the rotating drum and the stationary outlet is by circumferential “o” rings rather than by a face seal used on conventional valves.
- The clearance between the drum deck and the agitator on conventional drum filters is sufficient to accommodate cakes of up to about 50 mm while on modern Precoat filters higher clearances to allow the formation of 150 mm Precoat are quite common.
Dosing System
EIMCO-KCP offer Auto and Manual Dosing Systems for dosing coagulants like Lime, Ferrous Sulphate, Polyelectrolyte, Alum and Acids etc. Dosing systems are compact and rugged, engineered to handle and work efficiently under highly corrosive and varying conditions.
The dosing of water treatment chemicals needs to be precise if effective control of water treatment parameters is to be achieved. We have considerable experience in the selection of suitable dosing equipment. Years of water treatment experience means we can advise our customers on chemical dosing and help our customers ensure that their water treatment regime is operating as efficiently as possible.
Bar Screen
Bar Screens are designed for the continuous operation and it provides continuous free racking of the vertical screen grid by means of parallel raking beams.
Each bar is carried over on twin endless chains.
Eimco-K.C.P raked bar screens are very well suited for removing suspended and floating coarse debris such as weed, reed, rags etc., from surface water. These raked bar screens are particularly suitable for use in:
- Cooling water inlets
- Pumping stations
- Effluent treatment installations
The various types of bar screens are of robust design and made of high grade materials.
Vertical screens are arranged across the channel and dead plate fix area is between the top of the bars and it is the discharge point of the debris.
At the discharge point wiper blade to push the debris is fixed and it is fallen to the discharge chute.
Grit Separators
The EIMCO-K.C.P Grit Separator is recommended for general application on all sizes ranging up to 60 foot square. Sewage enters uniformly through adjustable deflectors along one side of the square tank and after depositing its grit overflows a weir at the opposite side, substantially free of grit.
Purpose: The Purpose of the EIMCO KCP Grit Removal scheme entails the following goals:
Grit Removal: Provide a flexible flow sheet to remove any desired mesh up to 1500 mesh grit so that protection of centrifuges and heat treatment equipment is possible.
Grit Conveyance: Use a reliable and rugged means to convey grit from the grit chamber underflow to the grit dewatering and washing equipment
Grit Dewatering: Provide a dewatering mechanism which is flexible with respect to desired mesh separation and operation location.
Grit Incineration: Design a system that will provide grit incineration and ultimate disposal of a nuisance.
Aerators
Fixed and Floating types /Low Speed & High Speed.
The EIMCO-K.C.P Fixed and floating mechanical surface aerators are available for any industrial waste treatment application.
The EIMCO -K.C.P Aerator is a highly efficient mechanical surface aerator for transferring oxygen from the atmosphere into wastewater. At the same time it provides vigorous agitation and mixing in the water to disperse the oxygen and keep solids in suspension, it is used in the Waste Water Treatment application also.
Oxygen transfer capacity of the aerator is high, ranging from 1.4 – 1.8 kg per impeller BHP hour, depending on the site conditions. High bottom velocities are also maintained. Our Aerators are provided with special gear reducers with respective motors and designed for high moisture corrosive environment also.
Fixed Aerators are fixed on the fixed platform and bridges, in case of floating; Aerators are fixed on the floating platforms.
Aeration testing facility
As a leader in Industrial technology, we take pride in Oxygen transfer testing for Aerators up to 100 HP. We have developed test pond and procedures to perform the necessary analysis to meet both customer approvals and industry regulations.
From scale-up tanks to full-scale aeration testing with R&D lab comprising advanced instruments to provide precise Oxygen transfer results and power consumption of impeller. This will result in equipment upgrades, process improvements, and comparative studies.
Our aeration equipment has undergone rigorous testing and has been proven to produce guaranteed results. Using our in-house test tank we will be able to provide service of Aerator testing for interested parties.
Mixer / Flocculator
EIMCO-K.C.P. Flocculator provides agitation for treating process liquids, water or wastewater in circular or square tanks. Available in 1 to 25 HP for chemical mixing and blending coagulants, neutralization and general purpose mixing. When used for flocculation, the unit has extremely high circulation capacity up to 25 times the feed rate. EIMCO-K.C.P. has other types of horizontal and vertical paddle flocculators available for flocculating and mixing applications.
Causticizing System
CAUSTICIZERS
Heavy duty agitators are generally used with the tank being heavy mild steel plate with a good lining. The agitator’s shaft & impellors will be of stainless steel construction.
LIME SLAKERS
EIMCO-K.C.P. Slakers and Slaker-Classifiers for lime are available in different sizes depending on the application and requirements. Slaker-Classifier combines the slaking action, classifying and grit removal in a single unit. The design provides adequate retention time for optimum slaking efficiency.
GREEN LIQUOR CLARIFIER
EIMCO-K.C.P. Green Liquor clarifier is designed to give better effluent clarification than the older multiple tray design at a lower installed cost. This unit can also be furnished with provisions for clarified Green Liquor Storage in same unit, thereby eliminating the extra tankage for green liquor storage capacity.
DREGS MIXER
Dregs Mixer is also available which operate on the same mechanism.
DREGS FILTER
Dregs Filter is also available which operate on the same mechanism.
WHITE LIQUOR CLARIFIER
A unit of tray type is used for White Liquor Clarification. Since maximum underflow density & clear white Liquor are the primary objectives, the unit type clarifier has obvious advantages. The peripheral overflow launder will insure minimum turbidity in the clarified white liquor & storage of solids to insure maximum underflow density where space is at a premium, a two of four compartment white liquor can be used.
LIME MUD WASHER
The Under flow from the white liquor clarifier must be washed to recover NA 2O values in it. Two stages washing is usually employed in a washer type tray thickener.
LIME MUD FILTER
EIMCO-K.C.P. lime mud filter is used to dewater the mud to the minimum moisture content & if necessary provide some additional washing of soda removal prior to feeding the mud into the kiln. The filter can be operated with complete cake discharge or as a Precoat using a heel of mud on the drum as a Precoat.
Lime Slacker Classifier
EIMCO-K.C.P. Slacker-Classifiers are used in preparation of Milk of Lime and Causticizers preparing for producing white liquor clarifier are available in different sizes depending on the application and requirements. Slaker-Classifier combines the slaking action, classifying and grit removal in a single unit. The design provides adequate retention time for optimum slaking efficiency.
EIMCO-K.C.P Slaker Classifiers are available depending on the design of the hot lime facilities.
The recommended Slaker Classifier combines the slaking action, classifying and grit removal in a single, rugged unit. An axial flow turbine in a baffled compartment is used for complete agitation. Better pumping action is achieved with a lower horsepower requirement.
The classifier section utilizes Rake Classifier, similar to that which has been successfully used in the metallurgical industry for many years. Virtually all of the plus 65 mesh inert solids are removed in this compartment. The grit is sprayed with water at the top of the screw to recover any remaining soda values before discharge.
The large diameter screw in the Classifier has a force lubricated lower sleeve, using either water or green liquor as the lubricating fluid.
The entire unit is heavy-duty construction with stainless steel used in the slaking compartment liners, the agitator shaft and impeller, overflow, feed piping, and the classifier rake.
The design provides for adequate detention time for optimum slaking efficiency.
Rotary Distributor
Flow is introduced at the center of the unit and is distributed by means of two or more rotating arms with orifices and spreaders. Hydraulic power created by the reaction of the jet-like streams escaping from the orifices is sufficient to rotate the machine. A spreader is provided at each orifice to uniformly distribute the flow in the thinnest possible sheet over the entire filter area.
The general type of rotary distributor recommended is determined by the proper combination of flow and head requirements. Center assembly designs are suitable for standard or high rate applications, with or without flow control features. Distributor arms are of circular pipe construction or may be fabricated from steel plate with single or multiple compartments.
The EIMCO-K.C.P Rotary Distributors are furnished for all bed sizes and with center inlet diameters from 8 in. to 54 in. Feed arrangements may be above or beneath the filter floor depending on media depth and flow transition requirements. The height of the center well is varied according to the head required and support for the distributor arms is provided by either tie rods or trusses.
CENTER ASSEMBLIES
SINGLE AND DOUBLE COMPARTMENT FOR VARIOUS FLOW AND HEAD CONDITIONS
The EIMCO-K.C.P Rotary Distributors are furnished with one of two center assembly designs. These include a basic standard or high rate assembly with no internal flow division features, and a high rate assembly with an internal annular weir for flow division.
DISTRIBUTOR ARMS
SINGLE AND DOUBLE COMPARTMENT PIPE OR RECTANGULAR TYPES
The EIMCO-K.C.P Rotary Distributors are available with circular pipe arms, fabricated rectangular arms or fabricated rectangular multiple compartment arms. The diameter of the filter, the influent flow and the available hydraulic head will normally determine the type of arm to be used.
DESIGN FEATURES
TURNTABLE BEARING, BASE CASTING, SEAL AND SPREADERS
Reliability and simplicity of the main bearing assembly are the key operating features of EIMCO KCP Rotary Distributors. The lower turntable type bearing is used on all distributor mechanisms, regardless of size. The large diameter ball bearings with hardened races are located close to the media face for stability against tilting.
The bearing runs in an oil bath. The only required maintenance is the seasonal oil change (where weather conditions require) plus occasional checking to maintain the proper oil level as indicated on a sight gauge.
The stationary base and revolving turn- table are of sturdy cast iron construction and are free of projections in the bottom center inlet opening which might obstruct the flow. Clearance between the turntable and base
is kept to a minimum. This guard against the possibility of the mechanism tipping.
A neoprene seal is provided to prevent leakage between rotating and fixed parts. This seal is economical, has a long life and requires no maintenance or special attention. The seal plate is readily accessible and easily replaced.
Diaphragm Pump
EKDS Pumps sturdy construction guarantees it will pump sludge and scum that no other unit can handle and will efficiently transfer anything that moves through a pipe.
The EKDS Pump can be automated to meet capacity and process requirements for maximum process efficiency.
The EKDS Pump’s construction allows it to be operated dry indefinitely. It cannot air bind, has no stator to burn out, and no seal to fail. The EKDS Pump is adjustable while in operation for maximum flexibility of both the capacity and discharge pressures. The EKDS Pump is a low maintenance pump.
Pump Capacity Range – 4.5 to 20.5 Cu.m./hr @ 60 m Head
Reactor Clarifier
THE EIMCO-K.C.P. LTD Solids Contact Reactor Clarifiers are basically divided into two different classes HRC and HRB mechanisms.
HRC is the high rate column supported Reactor Clarifier of size ranging from 15m to 75m diameters. HRB is a high rate bridge mounted Reactor Clarifier supplied in sizes ranging from 3m to 25m diameters.
- The high rate Solids-Contact Reactor Clarifier operates with the raw influent liquid being brought into immediate contact with a large circulating volume of relatively dense previously formed flocculate and precipitate.
- The mixture of raw influent liquid and re circulated slurry is sent upward into the reaction cone with 75-90% being returned to recirculation with the incoming raw water.
- The remaining 10-25 % passes under the cone and into the clarification zone. Once in the clarification zone, the solids settle to the tank floor with the clarified liquid moving into the effluent launder and exiting tank
The BFR and CF Reactor Clarifiers are applied to processes where longer detention times within the feed well and no solids recycle are necessary or requested by customer. The detention times are considerably longer than those offered by higher rate solids-contact units and are necessary for proper flocculation.
Lamella Clarifier
Description:
- THE EIMCO-K.C.P. LTD Lamella Clarifiers is a type of settler designed to remove particles from liquids.
- Lamella Clarifier of size ranging from 5 m to 20 m diameters.
- Lamella Clarifier is used in unlike clarifiers they use a series of inclined plates, these inclined plates provide a large effective settling area for a small footprint.
- Lamella clarifiers can be used in a range of industries including Industrial water treatment, mining, desalination plant and metal finishing, as well as used to treat groundwater, industrial process water and backwash from sand filters.
- Lamella clarifiers are ideal for applications where the solids loading are variable and solids sizing are fine and are more common than conventional clarifiers.
Advantage:
- The main advantage of lamella clarifiers over other clarifying systems is the large effective settling area caused by the use of inclined plates, which improves the operating conditions of the clarifiers in a number of ways. The unit is more compact usually requiring only 65-80 % of the area of clarifiers operating without inclined plates. Therefore, where site footprint constraints are of concern a lamella clarifier system is preferred.
- Lamella clarifier performance can be improved by the addition of flocculants and coagulants. These chemicals optimise the settling process and cause a higher purity of overflow water by ensuring all smaller solids are settled into the sludge underflow.
Brine Clarifier
EIMCO-K.C.P.Circular Clarifier are the most common type of sedimentation basin used for separating suspended solids from liquids in the treatment of water, sewage, Industrial waste and industrial process.
EIMCO-K.C.P. Offers Bridge mounted (B) type, Column Mounted (C) Type and Traction driven (T) type Classifiers mechanism for various applications. These operate on the common principle of moving settled solids to the center of principle of moving settled solids to the centre of the tank for removal, and differ principally in the method used to support and drive the rotating sludge removal arms.
EIMCO-K.C.P. Classifiers are designed to handle variety of applications & flows and clarifier includes scum skimming device to remove the floating material.
- Primary Clarifiers.
- Secondary Clarifiers.
- Brine Clarifiers for Caustic Soda Industries.
- FGD
- Reactor Clarifiers.
- White Liquid Clarifiers & Green Liquor Clarifiers for Pulp & Paper Industries.
- Lamella Clarifiers.
Registered Office
The EIMCO-K.C.P.
Ramakrishna Buildings No. 239,
Anna Salai, Chennai 600 006,
India
ekcp@vsnl.com, info@ekcp.com
(91-044) 28555171
Factory Address
The EIMCO-K.C.P. 11-A,
3rd Main Road Industrial Estate,
Ambattur, Chennai-600058, India
works@ekcp.com
(91-044) 28555171
You may also be interested in this heavy engineering fabrication company:

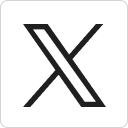




One thought on “EIMCO – K.C.P. Ltd”