Electrodrive Powertrain Solutions Pvt. Ltd. or Electra EV is India’s leading electric vehicles powertrain solutions (EV Charging Stations) company, focused on accelerating the future of electric mobility in India. The company offers relevant and affordable EV powertrain solutions, systems, and services to support OEMs, orchestrators, and tier-1 suppliers. Electra EV also works with global electric mobility providers to enable optimized EV powertrain solutions for Asian markets.
More than twenty-five percent of the total electric four-wheelers on Indian roads, in FY20, have an Electra EV powertrain inside them.
As a specialist company in the electric vehicle powertrain market, Electra EV is continuously innovating to bring new solutions to the forefront in its core areas of powertrain optimization and energy utilization. The company does this through designing, developing, and adapting electric powertrain technologies and by utilizing a systems approach to arrive at range and torque requirements in real use case scenarios. Electra EV also indigenously manufactures EV Powertrains, supplies and services them all over India.
Electra EV also leads the charge with industry partners and research consortia, working on various battery chemistries for range and life extension.
The company is headquartered in Pune with manufacturing facilities in Coimbatore.
In May 2021, Electra EV was awarded ISO 9001:2015 QMS certification by TÜV SÜD South Asia. The company’s Coimbatore location has been certified for ‘Design and Manufacture of Electric Powertrain for Automotive Drive Application’, and the Pune location for ‘Design, Development, and Marketing of Electric Powertrains’. Electrodrive Powertrain Solutions is the 1st Independent Pure-Play EV Powertrain Company in India with organization-wide ISO 9001:2015 certification.
EV POWERTRAIN SOLUTIONS
Battery Systems EV Charging Stations
Engineers from Electra EV use a unique combination of digital technologies and experimental use case data to develop Battery Systems, enabling superior energy management for EVs in a safe, reliable, and affordable manner.
Electra EV engineers have developed battery systems utilizing LFP and NMC battery packs for a variety of EV applications. These systems utilize a superior understanding of powertrain requirements, energy efficiency, and power electronics to create EVs with enhanced cumulative mileage, better thermal management, and overall vehicle performance.
An electric vehicle battery is often composed of individual cells arranged in a series/parallel configuration to achieve the desired voltage and capacity in the final pack. Cells/batteries are selected based on the requirements of the customer and vehicle requirements as per the automotive standard. Engineers from Electra EV achieve cell interconnections that reduce internal resistance losses significantly. The battery design complements the requirements of the motor(s) and charging system that a vehicle utilizes.
Battery systems from Electra EV come with a heating and/or cooling unit (Chill forced air / Liquid) to maintain thermal management and enable optimum life of the battery pack. This system is validated by either drive cycle or fast charge scenarios with different environment temperatures.
Battery systems are subjected to stringent validation and tests for automotive regulations like Crash, Vibration, Range test & Accelerated life tests, etc. Electra EV enables support for Validation and homologation through internal facilities and/or through a partner ecosystem.
Engineer at Electra EV utilizes the latest CAE, CFD, and modeling software to conduct efficiency mapping, before selecting components for such battery systems.
Electra EV battery systems comply to all relevant automotive safety standards.
The battery testing facility at Electra EV is well-equipped with cutting-edge essential equipment such as module life-cycle testers, battery-pack LCTs, battery analyzer, IR tester, and DC programmable electronic load.
Electra EV also collaborates with academia and other research consortia, working on various battery chemistries for range and life extension.
Battery Management Systems (BMS) EV Charging Stations
Battery management systems from Electra EV meet and exceed performance when it comes to critical features such as voltage, temperature, and current monitoring, battery state of charge (SoC), and cell balancing of lithium-ion (Li-ion) batteries.
Below are some of the features of BMS from Electra EV
- Individual voltage monitoring up to 36 channels
- SOC/DOD/SOH calculation
- Cell Temperature monitoring
- Cell Balancing – Active/Passive
- Charge control
- ISO 26262 functional safety
- SAE J1939 (commercial vehicles)/ ISO 11898 CAN communication Protocol
- Configurable software
Battery Tests during Production EV Charging Stations
Engineers from Electra EV ensure robust battery performance with the superior deployment of critical production tests. Capacity tests for discharge and charge, high rate discharge test to check electrical and mechanical integrity, SOH evaluation with Internal Resistance Measurement, Fast Charging Function and Performance testing, and stringent End of Line test for battery packs are a few of the comprehensive list of test areas in which Electra EV has acquired high levels of maturity.
Traction Power & Control Systems EV Charging Stations
Electra EV offers customized traction power & control systems for various types of vehicles ranging from 48 to 750 Volts.
Robust, energy-efficient torque control with traction systems developed by Electra EV has enabled performance improvement for a wide range of electric mobility applications
It is imperative for EV traction power and control systems to meet a multitude of operating requirements such as power, variable speed, operating voltage of the battery system, torque and speed combinations, physical space constraints, cost limitations, climatic conditions, and more.
Engineers from Electra EV have innovated to create relevant solutions for power optimization at different levels. The company offers customized design & development solutions for gearbox and motors both for Light & Heavy Vehicles, meeting FAME II criteria.
An EV is energy management in motion and a lot has to be taken care of well before the traction system can be developed and manufactured. Engineers from Electra EV apply their extensive understanding of traction systems and their functioning for application-specific design and tuning of overall performance. While electric vehicles have the distinct advantage of quick and precise torque generation, Electra EV specialists apply new control methodologies to boost performance. Electra EV also innovates to provide unique solutions integrating advanced power electronics into traction systems. In addition to the Motor Testing Lab, the Power Electronics Lab at Electra EV is well-equipped with the latest equipment to support development activities.
Single-speed gearboxes from Electra EV come with the guarantee of precision engineering to eliminate additional noise.
Effective End-of-Line testing ensures the complete elimination of any stray cases of noise in the final product.
The end goal, at all times, is to ensure that the most appropriate application is available with OEMs and fleet owners for their end customers.
Traction Units & Gear Boxes from Electra EV EV Charging Stations
AC Motors used in the Drive system integrated with Generator to produce energy during braking. The technology is selected and configured as per tech spec and pricing.
- Motors ranging from 48 – 750V
- AC Induction and Permanent Magnet (IP65)
- Air-cooled and liquid-cooled
- 4.5 KW to 180 KW Peak Power
- 4 Nm to 4500 Nm Peak Torque
- Indigenously designed single-speed gearbox capable of withstanding peak torques as per the application.
EV Powertrain Manufacturing & Series Production
Electra EV is an EV solutions company with unique expertise in the design, development, assembly, and manufacturing of state-of-the-art powertrains for electric mobility applications.
While the Design & Development (D&D) center at Pune facilitates design innovation, the manufacturing facility at Coimbatore along with the global supply network helps to bring unique powertrain solutions to life in an optimum time frame.
Presently, Electra EV is equipped to produce up to 300-500 powertrain kits a month, comprising Battery Systems, PDUs, and Drive Train assemblies along with required peripheral assemblies such as Fast Charge cables, Normal Charge Port Connector Assembly, Compressors, and Emergency Switch Assemblies.
The facility at Coimbatore has 30000 SFT dedicated to manufacturing and storage, scalable up to 500 kits per month with the current infrastructure.
The production setup at Electra EV is ready with all the necessary equipment to build high-quality powertrains consistently. The complete End-of-Line (EOL) test equipment facilitates qualification of key components and assemblies, process control, and final product acceptance for both software and hardware, electrical and mechanical components.
Electra EV is poised to be a global destination for outsourced powertrain manufacturing in EV and similar segments, including indigenization of global EV subsystems and components while leveraging India’s engineering talent and a local supply chain. Electra EV’s journey to localization follows the GOIs Phased Manufacturing Programme(PMP), thereby making it one of the few FAME compliant powertrain companies. Currently, the manufacturing and QA teams are preparing for ISO 9000 and IATF assessment and certification.
Series Production Capabilities EV Charging Stations
Battery System Manufacturing
The Battery Box assembly facility is equipped with the required chargers, dischargers, test and measuring equipment for incoming materials, in-process checking and final battery assembly testing for batteries, battery management systems, voltage and temperature sensing components,
fast/slow chargers and discharge capability testing et al. A strict protocol of battery assembly testing ensure adherence to strict quality assurance guidelines and practices, test methods, and Standard Operating Procedures ( SOPs).
PDU and Electronic Manufacturing
The PDU and Electronic assembly facility is equipped to produce complete power train constituents such as Battery Management Systems, Vehicle Control Systems, Motor Control systems. The facility adheres to strict quality assurance methods and practices for inward components, in-process control, and the final product, with sophisticated measurement equipment and gauges. A specially developed and established EOL with vehicle test equipment ensures that complete control systems are fully tested before delivery for hardware reliability and software integrity.
Drive Train Manufacturing
The drivetrain manufacturing facility has precision assembly equipment such as ultrasound cleaners, Hydraulic assembly equipment, metrology equipment, and End of Line Test equipment for the assembled Drive Trains. Each Drive Train undergoes strict checks for motor and gearbox performance, noise levels, and functional performance.
Electra EV is one of the pioneers in India when it comes to full solution capabilities in EV Design and Development. The company’s specialization in powertrains bore fruit in the year 2017 with the successful electrification of the Neo (Nano) for Ola Cabs. Electra EVs efforts led to the birth of a new zippy 48V system, completely designed and developed in India. Later, Electra EV developed 72 V powertrains for the Tigor EV(140 KM range) and the Tigor EV Extended Range (213 KM).
The Tata Ace EV for the Indian market will also have an indigenously developed powertrain from Electra EV.
Additionally, a number of manufacturing programs for innovative and exciting EV powertrains are ready for take-off at Electra EV.
PRODUCTS & SERVICES EV Charging Stations
Battery Electric Vehicles (BEVs) will lead the charge for electric mobility globally.
The Bloomberg NEF Electric Vehicle Outlook 2020 estimates that by 2040, over half of all passenger vehicles sold will be electric. A sizeable portion would be Battery Electric Vehicles. The total number of EV models globally is expected to number 500 by 2022. In the days to come, the combustion engine and powertrain will no longer be the default workhorse for mobility. While the numbers indicate the growing importance of electric mobility in days to come, mitigation of global warming is an even bigger reason to create bespoke EV platforms for diverse applications rapidly.
Electra EV is continually pushing the boundaries of powertrain development with innovative services and products. The company does this through designing, developing, and adapting electric powertrain technologies and by utilizing a systems approach to arrive at range and torque requirements in real use case scenarios. Electra EV also indigenously manufactures EV Powertrains, supplies and services them all over India.
Products
Battery Packs | Traction Units | Vehicle Control Unit | On-Board Charger | Vehicle Chargers | Telematics
Services
Traction System Design & Development | Prototyping | Homologation Readiness | After-Sales Services & Diagnostics
Traction Units EV Charging Stations
Traction units from Electra EV meet stringent torque and speed demands while enhancing performance
Electra EV develops motors for EV applications ranging from 48 to 750 Volt systems, finding optimal solutions in the face of conflicting constraints such as performance efficiency and safety considerations.
Efficient Traction Motors from Electra EV meet stringent load requirements, performance specifications, and operating environment restrictions.
The Electra EV Motor Testing Lab is equipped with a wide array of latest equipment and technology such as Motor-Dyno setup, DC power supply, power analyzers, and algorithms to map motors characteristics.
Traction Units from Electra EV
- Motors ranging from 48 – 750V
- ACIMs & PMSM (IP65)
- 4 Nm to 4500 Nm Peak Torque
- 5 to 180 KW Peak Power
Battery Packs EV Charging Stations
Engineers at Electra EV have been able to design a wide range of battery packs, with chemistries such as Lithium Iron Phosphate and Lithium Manganese Cobalt, depending on product requirements.
Lithium-Ion Battery (LIB) packs from Electra EV have been tested as per AIS 048 and certified by ARAI. LIB packs from Electra EV can operate at a wide range of temperatures ranging from sub-zero to 55 degrees C (drive).
Electra EV engineers are constantly striving to match and possibly exceed the performance of IC engine counterparts while retaining the useful life of respective powertrain systems.
Some of the key features of battery packs from Electra EV
- Scalable battery pack (48V – 750V)
- Robust Battery Management System
- Configurable BMS Software
- Heating and/or Cooling Unit
- IP67 protection
The Lithium Iron Phosphate (LFP) battery packs from Electra EV currently in use in the Indian market extend from 16.6 to 21.6 KWh, enabling a 200 to 213 KM driving range on a full charge. All the battery packs have been certified as per AIS 048 by ARAI. Electra EV battery packs use force chill air-cooled technology and integrate through an intelligent programmable BMS utilizing CAN communication network. The battery packs are currently in use in the Neo, Tigor EV, and Tigor EV (Extended Range) vehicles from Tata Motors.
In addition to the above, Electra EV has developed and manufactured full Battery Packs for 2Ws and a truck that would be launched by a new Indian OEM.
On-Board Charger EV Charging Stations
On-Board Chargers (OBC) from Electra EV meet requirements of high power density, high charging efficiency, and heat dissipation for a variety of electric mobility applications
The global electric vehicle On-Board Charger (OBC) market is estimated to reach $10.82 billion by 2027, registering a CAGR of 22.4% from 2020 to 2027. With OBCs that on average give 25% higher DC-DC rating and ~30% reduction in charge duration, Electra EV has been developing OBCs which have helped electric mobility applications exceed end-user expectations.
Electra EV chargers have been designed and optimized for robust performance in harsh tropical conditions
Electra EV has developed an in-depth understanding of EV batteries, combining vehicle data and analytics from service nodes as well as different chemistries to create suitable On-Board Chargers that integrate seamlessly with the EV Battery Management System and with Vehicle Management system, communicating through CAN.
Engineers at Electra EV are continuously innovating to create efficient, highly reliable, and compact chargers at different power levels suitable for Indian grid conditions.
Vehicle Control Unit EV Charging Stations
Engineers from Electra EV leverage their understanding of electric mobility applications to design and develop Vehicle Control Units (VCUs) that enable effective control strategies of all aspects of the EV powertrain.
The increasing demand for electric vehicles coupled with rising safety concerns, growing demand for advanced driver assistance systems (ADAS), and other automated safety systems is propelling the need for innovation in the area of VCU development. It is time for the development of the digital vehicle and the VCU would play an increasingly important role in shaping EVs of the future.
VCUs from Electra EV come with the guarantee of superior control strategies for charging control, high voltage coordination, and thermal management among other benefits. Engineers from Electra EV continuously analyze EV operation parameters vis-a-vis road conditions and other criteria to ensure that control unit designs are robust and adaptive, enabling system improvement in dynamic and steady-state performance.
Vehicle Control Unit (VCU) from Electra EV
- Fully indigenously designed and developed Vehicle Management Unit
- OS designed to configure parameters and build Diagnostics front-end
- In line with ISO 26262 functional safety, SAE J1939 & ISO 11898 CAN protocol and ISO 14229-1 UDS Protocol
Vehicle Chargers
Electra EV, in partnership with leading global charger manufacturing companies, can provide off-the-shelf as well as custom charging solutions for home and public use, complying with international standards. The Electra EV charger suite consists of compact, low-weight units, highly acclaimed for reliability and efficiency across a wide range of input voltage.
With the vision to accelerate the adoption of electric mobility, Electra EV has invested considerable resources for the development of power conversion solutions for a wide range of electric mobility applications. Specialists from Electra focus on software and hardware development to make the EV charging process efficient and safe for end-users.
Electra EVs expertise in developing sophisticated battery management systems comes in handy when building efficient vehicle charging solutions that preserve battery life while enabling fast charging. DC fast chargers from Electra EV adhere to Bharat EV Charger DC-001 as well as GB/T standards and are available for CCS/CHAdeMO/SAE J1772 protocols.
With 96% plus efficiency, the RangeXT/20 from Green-Motion – a partner to Electra EV – is one of the world’s most efficient chargers.
Charging solutions from Electra EV can include a comprehensive array of added features like authentication, integrated payment gateways, software for Remote monitoring, SMS, contactless near field communication, car park tickets, and more.
Vehicle chargers from Electra EV use the IEC 60309 Industrial Blue connectors, recommended by Bharat EV specifications.
Telematics
Electra EV partners with global providers to create best-in-class Telematics products and solutions for electric mobility applications in the fleet and personal mobility segments.
Fleet management systems offer immense value, helping reduce costs, improve efficiency, build security and ensure compliance across the fleet operation. However, it is important to choose the right telematics solution to ensure that electric mobility applications become part of a network that performs to their full potential.
Telematics solutions from Electra EV have enhanced overall product value for OEMs, fleet operators, and end customers in their respective areas of operation. Our solutions comprise Online Diagnostics enabled on Android and iOS apps.
A few of our solution features are as follows:
Telematics
- 2.5m GPS Accuracy
- Class 10 Reliable GPRS
- Zero Antenna Technology
- Panic Button Interface
- Motion Sensing
- RS232 Data Interface
- Immobilizer Interface with Built-In Relay Driver
- Opto Isolated General Purpose Inputs(Door Sensor, Seat Belt, and other peripherals)
Telematics Application (Mobile & PC)
- Fully functional Mobile App compatible with IoS, Android, and Windows
- Fully functional PC interface that can be accessed through the internet
It is interesting to note that Telematics solutions have been used internally by Electra EV for gathering driving data about Indian roads. Such data has been integrated into machine learning systems to improve and optimize the performance of EV powertrains.
Manufacturing Facility
Electra EV
#97/3, Trichy Road,
Vadakku Sambala Thottam,
Kanampalayam, Sulur Tk,
Coimbatore,
Tamil Nadu INDIA- 641 402
Corporate Office and Design & Development Centre
Opp India Land Global Tech Park,
Hinjewadi Phase 2 Road – Phase 1,
Hinjewadi, Pune, 411057
http://electraev.com/
You may also be interested in these manufacturers in the EV space:

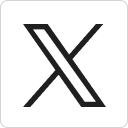




One thought on “Electra EV”