Savio now operates worldwide in the production and marketing of spinning mill, automatic winders, two-for-one twisters, and rotor spinning frames with manufacturing plants in Italy, China and India.
TWISTING
Savio is present since late 1950s in twisting technology, first with ring twisting machine FM280 in 1949, followed by the first two-for-twister in 1963. With a wide range of Two-for-one twisters diversified for different market requirements, Savio twisting machines respond to the demands of customers looking for a significant reduction in labor and energy.
Besides the demand to sustain low investment costs and lower energy consumption, the customers also take on great importance time and cost of maintenance. These models foresee: a high structural standardization, a wide range both for feeding and spindle dimensions for every yarn type and count, electronic solutions to simplify the operator intervention and reduce the maintenance workforce.
TWO FOR ONE TWISTER
SIRIUS – THINKING GLOBAL, ACTING LOCAL
Middle and Far East countries, that constitute the key Markets for Two for one Twisters, are today showing requirements that until now have characterized the Traditional western markets. The new needs are diverse, not only among each Market area, but also throughout a single Market.
The main requirement is to reduce workforce, which is becoming, day by day, more and more difficult to find, even if its costs are still strongly competitive if compared with the western markets. Moreover, apart from the need to reduce the initial investment costs as well as power consumption, a great number of Companies keep asking for products which can grant low maintenance times and costs. To meet those new requests, sometimes in contradiction one with each other, Savio has developed its brand new Two for One Twisters generation, Sirius, that is able to solve all the problems mentioned above.
FEATURES OF MACHINE
An high structural standardization for all the diverse models.
A wide range both for feeding and spindle dimensions for every yarn type and count.
A great optional offer, available for all the different machine versions.
Electronic solutions and simplified maintenance to reduce the workforce needed for each machine.
FEATURES OF SPINDLES
Life Lubricated top bearings, with special dustproof protection.
Stainless steel plate and compensating pulley in aluminum with a ceramic coating, with optimized shape that guarantees less power absorption and maximum feeding content.
Yarn tensioning with interchangable spring pistons for different counts and materials.
Tension can be adjusted with 6 different positions.
High flexibility thanks to quick transformation from free to controlled
In other words, with its new Two for One Twister, Sirius, Savio met the objective to put together needs that, until today, appeared to be alternative, offering a competitive global machine, that can, at the same time, be fitted according the local needs of each single market and client.
COSMOS – SIMPLE, RELIABLE STATE OF THE ART TWISTING
Cosmos represents another Savio proposal in the field of twisting to ensure maximum cost effectiveness of the technological process through constructional solutions that allow a reduction in investment with a minimum of energy consumption.The aim of all this is to maximize the productivity of the machine,the quality of the package and the twisted yarn, along with the technological flexibility, that is today an indispensable requirement for any textile market.
MACHINE PRODUCTIVITY
Range of spindles, with shapes and manufacturing techniques aimed at maximizing the weights of packages being fed, with different materials and counts, always giving priority to energy saving.
System of spindle rotation by means of two paris of bearings: the upper bearings, high performance, with upper protections and maintenance free lubrication;the lower bearings, lubricated with grease with separate external nipples.
Adjustments of twisting tension through a 6-Position adjustable system.
TECHNOLOGICAL FLEXIBILITY
The availability of different types of spindles makes it possible to optimize the production for the materials and different range of counts.
Balloon limiter(optional), which can also be installed subsequently, to maximize cost-efficiency of the process for different counts and weights of the packages being fed.
Special Flyer (optional) for twisting elasticized yarns and Waxing unit(optional) to prepare packages to be used for knitting
Bunching device(optional) for uniform tail end preparation
QUALITY OF YARN AND PACKAGE
Reduction of twisting tension through optimization of the shape of the balloon,obtained though a different layout of the elements that control it.
Accurate finishing and surface treatment of all parts that come into contact with the yarn.
Mechanical counterweight of package arm.System of modulation and distribution of the yarn on package, mechanical type.
Consolidated mechanical system of anti-ribboning, variable for types of different yarn and materials.
Self-cleaning of lower part of spindle by means of air ventilation
HIGH CONSOLIDATED TAKE-UP SYSTEM
The Mechanical cam system, for the distribution of the yarn on the spindle, for the modulation and cross angle, is housed in a centralized box, with oil lubrication activated by a special pump.
The pulleys for twist and overfeed are easily accessible from outside and controlled by high-performance, low-noise toothed belts.
WINDING
40% of worldwide yarn is controlled and certified by Savio’s automatic winding machines.
Since 1954 with “CSr” machine, the automatic winder represents Savio’s main product (85-90% of sales). The developments of the winding technology are reflected through the years with different machine model generations, each of them representing the utmost technology available. In 1983, Savio introduced RAS15 C/I, the first link winder appeared on the world market.
The previous success of the mechanical models has been followed by the last generation of the fully electronically controlled ones, which is today the state-of-the-art.
Being the bridge between the spinning and the downstream processes, the automatic winders must have high productivity output and assure quality control of yarn and package formation.
ECOPULSARS PLUS – BREAK-THROUGH INNOVATION WITH AN ECO-GREEN LEVERAGE
EcoPulsarS Plus, with its sustainable eco-green advantage, replies to the market demand of energy saving, including also room air conditioning, together with improved production performances, high quality packages and utmost flexibility.
The combination of all new features and design has created an environment in which each part of the machine can operate at its optimum level and without limitations. Spindles and bobbins feeding systems set independently the level of suction required. Suction is generated as needed and used without losses.
The new Controlled Cut System, Yarn Tension Control System, Waste Collection&Separation System and Upgraded Splicing Solutions, each contributing to the overall reduction of the process downtimes.
FEATURES OF MACHINE
Break-through innovation with an eco-green leverage.
Suction on demand system (S.D.S.) saves energy up to 30%.
Savings on humidification plant initial and running cost.
Cyclonic waste separator for Hard waste and dust.
Controlled cut system (C.C.S.) for reduced red lights, repeaters and hard waste.
Number of heads – No limits (for magazine feeding machine up to 120 drums).
Enhanced productivity up to 10%.
Yarn presence sensor (optional)
Multicone: the digital yarn layering technology
Multi Link – Classic or Underground Solutions
O.B.S. – Off Standard Bobbin Selector (optional)
S.I.S. – Savio Identification System (optional)
Package B-Grade System – Manual (optional)
Empty cones centralized magazine (optional)
Smart Industry Solutions for Textile Mills Savio Winder 4.0
P.T.S. – Package Tracking System (optional)
POLAR EVOLUTION I/DLS – AUTOMATIC WINDER
Savio’s well proven and the bestselling automatic winder, still the #1 winder in many world markets.
The Savio POLAR Evolution I/DLS , for linking the ring spinning frames to winders, enables a fast and efficient direct feeding of bobbins, along with the full interfacing flexibility with all kinds of ring spinning frames (single or multistep). Many important developing markets are investing on this kind of machinery, because of the growing difficulty of hiring labor, for the quality and production advantages that such solution offers. Therefore in all those countries, we are witnessing a rapid transformation from plants equipped with ring spinning frames without doffing devices and with free-standing winder, to the fully automatic link solution.
The POLAR Evolution I/DLS boasts a unique spinning frame to winder close loop feeding system, the winder being an extension of the same, ensuring total free flow of the materials. From ring frame bobbin to the final package, the yarn is processed untouched and with zero transit time, ensuring maximum quality, less material handling and no chances of contamination.
FEATURES OF MACHINE
Direct transfer of ring bobbins to winder.
Yarn end preparation stations up to 3, for the longest ring frame.
Automatic empty tube loader for empty caddies.
Spindle Identification System (S.I.S).
Multicone: the digital yarn layering technology
Upgraded splicing solutions – Duo Air Feeding system
Multi Link – Classic or Underground Solutions
O.B.S. – Off Standard Bobbin Selector (optional)
S.I.S. – Savio Identification System (optional)
Package B-Grade System – Manual (optional)
Smart Industry Solutions for Textile Mills Savio Winder 4.0
POLAR EVOLUTION M/L – AUTOMATIC WINDER
The developments and innovations on the winding process have been always dictated by the market requirements.
A successfull winding process has to reach the following targets:
To match the new technological requirements, in order to follow the continuous change of the yarns and fabrics structure requested by the new fashion trend;
A piece of equipment which represents a perfect combination of flexibility simplicity with high reliability and easy to be used.
FEATURES OF MACHINE
Robust single piece cradle for higher speeds.
Flexi Cycle for increased efficiency.
Energy efficient suction system for longer length machine up to 80 heads.
Splicer to suite all needs of industry (Air, Moist Air, Wet, Heat, mechanical Twinsplicer® and knotter).
Efficient and fast automatic doffer.
Bobbin feeding system – up to 450mm length & remnant cones up to 110mm dia.
VOLUFIL MULTICONE – THERMIC TREATMENT AND WINDING PROCESS ON A SINGLE MACHINE
The consolidated success of the “Volufil technology” and the new demand of different yarns for diversified fabric applications, have requested several new developments on the machine technology. The new Volufil Multicone represents the proper reply to the new markets requirements.
As matter of fact, Savio has extended the technological process on acrylic heat set yarns, on special yarns (chenille) and on traditional HB Acrylic fibers, also blended with wool and elastomeric filaments.
The new drumless winding system “Multicone” allows the best solution for any yarn type and package format with different traverse take-up. The Multicone technology allows the tailoring of package for different end use (dyeing, knitting, etc.) with simple settings on PC.
FEATURES OF MACHINE
Continuous shrinking and bulking and winding on single machine for manpower saving.
Linear traverse motion for digital yarn layering system.
Traverse up to 250mm, diameter up to 280mm for higher take up packages.
Innovating heating chamber for effective shrinking/ bulking operation with less maintenance.
Higher winding speed.
New gate type tensioning device for better yarn control.
Visual interface on the PC screen for almost tailoring the final package.
Winding speed up to 1.000 mt/min according to the required thermic treatment.
HELIOS – OPEN END ROTOR SPINNING MACHINE
Rotor spinning (commonly called “Open End spinning”) is a process that incorporates spinning and winding operations. With the Open End system, the sliver coming from the draw frame is directly transformed into yarn, wound onto package cones. In the count range in which it can be used, the use of the rotor spinning machine allows an abbreviated production cycle and greater production per unit.
BENEFITS
Modern Spinning Technology which meet all main requirements.
High spinning speed thanks to new Savio Spin box.
Reduced energy consumption.
Hybrid technology to optimize efficiency and flexibility.
HIGHLIGHTS
Full automated open-end rotor spinning machine with hybrid technology to optimize efficiency, minimum “non productive” time and to support high flexibility.
High spinning speed of up-to 125.000 rpm with new Savio spin box.
Take-up speed of up to 250 m/min.
Electronic package building.
Independent sides for two lots processing.
Minimizing energy power.
Low operation height makes the machine user-friendly for all kind of operations.
Up-to 520 spinning units to meet customers’ requirements and optimize their investment.
Savio India
Tamaraikulam P.O.,
Pollachi TK.
Coimbatore – 642 109. India
Phone : +91 4259 201500
E-Mail : mail@savioindia.in
https://www.savioindia.com/default.aspx
You may also be interested in this textile machinery manufacturer:
Veejay Lakshmi Engineering Works Limited
Spinning Mill, Spinning Mill, Spinning Mill, Spinning Mill, Spinning Mill, Spinning Mill, Spinning Mill, Spinning Mill,

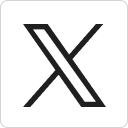



