GasFe Technology is an engineering organization specializing in the design, manufacture, and turnkey supply of Nitrogen Gas plants and hydrogen Gas plants.
Their product range includes:
- Batch/Continuous Oven as per the client’s requirement,
- Sintering, Heat treatment, vacuum sintering furnaces.
- Ammonia cracker.
- On- site Nitrogen and hydrogen Gas plants.
- N2/H2 Gas generators,
- Compressed Air Systems ‘CAS’.
- Gas & Moisture Analyzers.
- Air / Gas Storage Tanks.
- Leased Nitrogen Systems with Back up arrangements.
- Ammonia, LPG, Nitrous Oxide, helium manifold and accessories
- All type of Gas Lines and accessories
- All type Furnace Service and maintenance
NITROGEN GAS PLANT
PSA Nitrogen generation plant based on the PSA process consists of two absorbers filled with carbon molecular sieves, which have the property to absorb Oxygen from compressed air(CMS). Compressed and purified air is passed through the absorbers in this process.
Mainly oxygen is absorbed on the carbon molecular sieves as it has preferential properties for adsorption of moisture first and nitrogen-enriched gas is leaving the absorber. The oxygen concentration can be reduced to almost all required levels. During adsorption in one adsorber, the second adsorber is totally regenerated just by depressurization to ambient pressure. The oxygen-enriched off-gas is vented. After about one minute of adsorption in one adsorber, the process controller is switching over to the second adsorber to produce nitrogen on a continuous basis.
Technical Specifications | ||||
BASIC CMS | CMS HPN | CMS-Dx | CU-Dx Model | |
Oxygen | 0.1 to 2 % | 10-ppm to 500ppm | 1 to 3ppm(max) | 1-ppm (max) |
Nitrogen | 98-99.9% | 99.5 to 99.999% | Balance 99.9999% | Balance 99.9999% |
Hydrogen | Nil | Nil | 0.5% or more | Nil |
Dew Point | (-)60ºC to (-)80ºC | (-)60ºC to (-)80ºC | (-)60ºC to (-)80ºC | (-)60ºC to (-)80ºC |
Normal outlet pressure | 5.5bar | 5.5bar | 5.5bar | 5.5bar |
With Boosting outlet pressure | up to 60 bar | up to 60 bar | up to 60 bar | up to 60 bar |
Nitrogen generators have a wide variety of applications. From the Heat Treatment industry, oil & gas industry, mining, food packaging and storage, Electronics industry, Synthetic Fiber Industry, Their systems are designed to meet each customer’s specific purity, pressure, and flow requirements for a fraction of the cost of delivered gas.
HYDROGEN GAS PLANT Nitrogen Gas Plants
This method generates hydrogen through Electrolysis (bipolar type) along with gas boosters and de-oxo units. Electrolysis dissociates the elements of water (oxygen and hydrogen) by charging the water with an electrical current. The amount of power consumed by these plants is 4.5 KW (per cubic meter of hydrogen).
The hydrogen obtained is collected in a hydrogen gas holder and is further used for processing. Though hydrogen obtained through electrolysis is 99.8% pure, the use of de-oxo units helps in purifying it further (up to 99.999%).
In an electrolyzer, the symmetrical conductive structure is provided with the anode in the middle and cathode at ends that avoid the shortage of voltage. Though hydrogen obtained through electrolysis is 99.8% pure, the use of de-oxo units helps in purifying it further (up to 99.999%). The purified gas obtained after the process is used in heat treatment furnaces like annealing, sintering, and reducing furnace atmosphere.
Technical Specifications | |
Flow rate | 1 to 100 Nm3/ hr. |
H2purity | 98% – 99.99% |
Pressure | 5 – 25 bar g |
Dew point | up to (-60) deg C |
APPLICATIONS:
- Heat treatment, Hardening.
- Glass Melting
- Hydrogen Welding & Brazing
- Protective Atmosphere for Manufacture of Electronic Component
- Petroleum, chemical industries and electronic industry.
Technical Specifications;
- Flow rate 1 to 100 Nm3/ hr.
- H2purity 98% – 99.99%
- Pressure 5 – 25 bar g
- Dew point up to (-60) deg C
AMMONIA CRACKER Nitrogen Gas Plants
At GasFe Technology we cater to the needs of ammonia cracking units to domestic as well as international markets. As we know, the ammonia cracker gas unit produces a mixture of nitrogen and hydrogen which is usually used in heat treatment furnaces. We specialize in offering our range of Ammonia Crackers or Ammonia Cracker Gas Generator, which is commonly used to generate a mixture of Hydrogen and Nitrogen.
These are widely used in many industries for heat treatment furnaces and are easy to operate and require low maintenance. Ammonia cracking takes place on Nickel catalyst at 850 degrees C temperature. Around 100-ppm un-cracked ammonia is also present in cracked gas and its dew point is (-) 30 degrees C.
Process Description;
The cracking of ammonia is one of the most economical ways for on-site generation of hydrogen gas for industrial purposes. For this process, the temperature of 850 degrees C is maintained in the electrically heated furnace. A centrifugal cast retort is installed in the center of this furnace. This furnace is filled with a nickel catalyst. At this stage, the ammonia cracking takes place in presence of a nickel catalyst. The process separates its vital element into 75 % hydrogen and 25% nitrogen gas at a dew point of (-)30 degrees C.
In fact, nitrogen gas is generally inert. This mixture is treated as pure hydrogen gas. This becomes the most economical, trusted, tried, and dependable source of on-site hydrogen generation for many small and large industries. A molecular sieve purifier is used after the ammonia cracking unit for reducing residual ammonia content and to get very dry gas. This reduces ammonia down to 1-ppm level and dries gas up to (-) 80°C dew point.
Gas Composition | ||
Products | Without Purifier | With Purifier |
Hydrogen | 75% | 75% |
Nitrogen | 25% | 25% |
Oxygen | Nil | Nil |
Residual Ammonia | 100-ppm(max) | 1-ppm (max) |
Dew Point | (-) 30°C | Up to (-)80°C |
FURNACES Nitrogen Gas Plants
BATCH / CONTINUOUS FURNACE
GasFe technology Company’s furnaces provide improved control over time and temperature relations to achieve desired Metallurgical properties in such areas as Hardening, Tempering, annealing, Austempering, Brazing, Sintering, Curing, Drying. This can be applied to ferrous and nonferrous materials.
GasFe furnaces designed Temperature Range Of ambient to 1300°C.
GasFe can supply Batch / continuous Furnace For any Heat treatment applications, Chemical Drying, and Bulk Drug Applications.
FEATURES OF BATCH / CONTINUOUS FURNACES:
- Special Muffle Design
- Alloy Steel, Ceramics.
- Gas or Electric Heating
- GasFe technology Offers depending on customer Requirements.
- Monitoring & Control
- Supervisory control and data acquisition (SCADA) system.
BRAZING FURNACES
FEATURES OF BRAZING FURNACES:
- Alloy or Ceramic Muffle
- Muffle to help direct, control, and reduce atmosphere flow.
- May incorporate a silicon carbide muffle.
- This ceramic muffle is guaranteed for 5 years if used under recommended operating procedures.
- Straight or Humpback
- Both straight-through and humpback designs.
- Gas or Electric Heating
INDUSTRIAL OVENS Nitrogen Gas Plants
HOT AIR OVEN:
GasFe Technology is a pioneer in designing and manufacturing dryers for the various processes as for client Requirements. We are helping our clients with our engineering solutions for the last 20 years, our huge experience and commitment to quality had made us the first preference of clients for their need of heating, drying, or cooling. Till now we have manufactured various types of dryers by keeping the need of the client at front. We hold proficiency in designing and manufacturing dryers. Manufactured by our team of experts, these dryers are highly cherished by the Automobile, pharmaceuticals, foods, chemicals, and other Industries.
The air circulation is provided by the dynamically placed axial flow type blower fans in the drying chamber, during the process. The Control panel is provided with a process timer, digital temperature controller and indicator lamp, etc (Circular Chart recorder is provided at an extra cost and on-demand).
Applications:
For Automobile Industries, Chemical Industries, bulk Drugs Industries, and Painting Industries.
COMPRESSED AIR SYSTEM Nitrogen Gas Plants
Introduction to Compressed Air Systems
Compressed air systems consist of a number of major subsystems and components. Compressed air systems can be subdivided into the Supply and Demand-side.
The Supply-side includes compressors, air treatment, and primary storage. A properly managed supply side will result in clean, dry, stable air being delivered at the appropriate pressure in a dependable, cost-effective manner. Major compressed air supply subsystems typically include the air intake, air compressor (fixed speed and/or variable speed), aftercooler, motor, controls, treatment equipment, and accessories.
Controls serve to adjust the amount of compressed air being produced to maintain constant system pressure and manage the interaction between system components. Air filters and air dryers remove moisture, oil, and contaminants from the compressed air. Compressed air storage (wet and dry receivers) can also be used to improve system efficiency and stability. Accumulated water is manually or automatically discharged through drains. Optional pressure controllers are used to maintaining constant pressure at an end-user device.
The Demand-side includes distribution piping, secondary storage, and end-use equipment. A properly managed demand side minimizes pressure differentials, reduces wasted air from leakage and drainage, and utilizes compressed air for appropriate applications. Distribution piping systems transport compressed air from the air compressor to the end-use point where it is required. Compressed air storage receivers on the demand side can also be used to improve system pressure stability.
As a rule of thumb, for every horsepower (HP) in the nameplate capacity, the air compressor will produce approximately 4 standard cubic feet per minute.
Compressed Air Use;
Compressed air is used for a parse range of commercial and industrial applications. As it is widely employed throughout the industry, it is sometimes considered to be the “fourth utility” at many facilities.
In many facilities, compressed air systems are the least energy-efficient of all equipment. There is a tremendous potential to implement compressed air energy efficiency practices.
It has been common practice in the past to make decisions about compressed air equipment and the end uses based on a first cost notion. Ongoing energy, productivity, and maintenance costs need to be considered for optimal systems. In other words, best practice calls for decisions to be based on the life cycle cost of the compressed air system and components.
Improving and maintaining peak compressed air system optimization requires addressing both the supply and demand sides of the system and understanding how the two interact.
Properly managing a compressed air system can not only save electricity, but also decrease downtime, increase productivity, reduce maintenance, and improve product quality.
Optimal performance can be ensured by properly specifying and sizing equipment, operating the system at the lowest possible pressure, shutting down unnecessary equipment, and managing compressor controls and air storage. In addition, the repair of chronic air leaks will further reduce costs.
For a typical compressed air end use, like an air motor or diaphragm pump, it takes about 10 units of electrical energy input to the compressor to produce about one unit of actual mechanical output to the work.
For this reason, other methods of power output, such as direct-drive electric motors, should be considered first before using compressed air-powered equipment. If compressed air is used for an application, the amount of air used should be the minimum quantity and pressure necessary, and should only be used for the shortest possible duration. Compressed air use should also be constantly monitored and reevaluated.
SPARES AND ACCESSORIES Nitrogen Gas Plants
- Radiant Heaters
- Coil Heaters
- Strip Heaters
- Alloy Radiant Tubes
- Ammonia Cracker Retort
- Water Cooling Jackets
- Buffer Tanks
Gasfe Technology
N0, 40 Jaya Nager,
Jaya Nagar Main Road,
Thiruvallur,
Pin Code – 602001
09381344242/08778939763
info@gasfetechnology.com
https://www.gasfetechnology.com/
You may also be interested in these manufacturers:

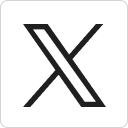




One thought on “GasFe Technology”