For more than 30 years, Dongwoo has been serving customers with software and hardware in the field of heat treatment including Aluminum Melting Furnace, plasma coating, and other surface engineering techniques equipped with state-of-the-art machinery for heat & surface treatments.
Industrial Furnace Division
- Batch Type
- Continuous Type
- Mesh Belt Type
- Rotary Type
- Vacuum Type
- Pit Type
- Aluminum Melting Furnace
- Aluminum Heat Treatment
- Steel Industrial
- Additional Equipment
Commercial Heat Treatment Division
- Carburizing
- Nitriding
- Quenching & Tempering
- Induction Heat Plug Quenching
- Austempering
INDUSTRIAL FURNACE DIVISION
BATCH TYPE Aluminum Melting Furnace
Pusher Type Aluminum Melting Furnace
A typical batch-type heat-treating furnace. Maintains stable atmospheric conditions while workpieces are transferred. Best-selling heat-treating furnace due to its convenience and proven quality over time.
Process Options
+ Carburizing, Carbonitriding, Bright Quenching, Annealing
Roller Type Aluminum Melting Furnace
A typical batch heat-treating furnace. Provides stable atmospheric conditions while workpieces are transferred inside of the furnace. Best-selling heat-treating furnace due to its convenience and proven quality over time.
Roller style requires less room than a pusher furnace and handles smaller weight, so is suitable for mid-range weight charges.
Process Options
Carburizing, Carbonitriding, Bright Quenching, Annealing
Semi-continuous Batch Type Aluminum Melting Furnace
Continuous heat-treating furnace based on the batch-type furnace. Guarantees more than twice the level of productivity than a standard batch furnace. Fully automatic, and provides stable atmospheric conditions while workpieces are transferred inside of the furnace.
Three-room type semi-continuous batch furnace consists of pre-heating, main heat-treating furnace, and quenching tank. Both oil and salt can be chosen as required by the piece being produced.
Process Options
Carburizing, Carbonitriding, Bright Quenching, Annealing, etc.
In & Out Type Aluminum Melting Furnace
IN-OUT type was developed specifically to use the smallest possible space.
Time loss between the charges has been significantly reduced, as the workpiece is charged as soon as the previous one is quenched.
Process Options
Carburizing, Carbonitriding, Bright Quenching, Annealing
Austempering Aluminum Melting Furnace
A convertible heat-treating furnace handles both standard processing and austempering as required by the product.
Process Options
Carburizing, Carbonitriding, Austemper, etc.
CONTINUOUS TYPE Aluminum Melting Furnace
Semi Continuous Type Aluminum Melting Furnace
Requires less room than a continuous batch furnace, with a fully automatic continuous heat-treating process designed to maximize productivity for your site.
Provides stable atmospheric conditions while the workpiece is transferred inside the furnace.
The semi-continuous batch furnace consists of inserting, pre-heating, heat-treating furnace, and quenching with oil (or salt) storage tank.
Supplementary installation of pre-washing, washing, or tempering furnace also available.
Process Options
Carburizing, Carbonitriding, Bright Quenching, Annealing, etc.
Continuous Type – Roller Type Aluminum Melting Furnace
Continuous furnace consisting of inserting, pre-heating, heat-treating furnace and quenching, with oil (or salt) storage tank.
Supplementary installation of pre-washing, washing, or tempering furnace also available.
Roller systems can vary from the linear formation of pusher-type furnaces, reducing transferring issues and requiring 40% less floor space. No need for an empty tray insert for charging and discharging.
A different workpiece with an alternate heat-treating pattern can be input while the furnace is treating other workpieces.
Suitable for workpieces that require a long heat-treating period and high quality.
Continuous Type – Push Type Aluminum Melting Furnace
Continuous type furnace consists of charging, pre-heating, heat treating furnace and quenching, with oil (or salt) storage tank. Supplementary installation of pre-washing, washing, or tempering furnace also available.
Suitable for the workpieces that require a long heat-treating period and high quality. Widely chosen for its easy maintenance.
Process Options
Carburizing, Carbonitriding, Bright Quenching, Annealing, etc.
MESH BELT TYPE Aluminum Melting Furnace
Carburizing (QT) Aluminum Melting Furnace
Continuous heat-treating mesh belt furnace consists of charging, pre-cleaning, quenching furnace, oil tank, mid-cleaning, tempering, and discharging furnace.
Specialized for mass production of small items such as bolts and bearings.
Both carburizing and Q/T can be done in full automatic following the mesh beltline.
Austempering
Continuous mesh belt furnace especially designed for austempering automotive parts. Consists of charging, pre-cleaning, quenching/salt tank, mid-cleaning, drying furnace, and discharging furnace. Mostly heat-treating chainplate for automotive parts.
The fully automated process following mesh beltline.
Process Options
Austemper, martemper, quenching, tempering, salt quenching, Non-oxy quenching
ROTARY TYPE
Carburizing
Energy and space-saving rotary type continuous heat-treating furnace. A fully automated process on a turntable drive.
Al Heat Treating
Fully automated rotary furnace using turntable and robot arm loading and unloading mechanism.
The favorable choice for solution treating and aging of large aluminum parts such as cylinder block, cylinder head, and wheels. Better heat distribution with a gas burner and a large fan in a circular structure.
VACUUM TYPE
One Chamber Type
The low-pressure atmosphere for heat treating is quenched in the same position. Easy control and maintenance.
Two Chamber Type
Separated chamber for heating and cooling. Higher cooling efficiency than a single chamber. Various types of heat treating are possible for different demands.
Either gas or oil cooling can be chosen depending on the size of the workpiece and the heat-treating method. Cooling pressure with gas can be operated up to 10 bar.
Vacuum Carburizing
Non-equilibrium, boost-diffusion carburizing process in which steel being processed is austenitized in a rough vacuum, carburized in partial pressure of hydrocarbon gas, diffused in a rough vacuum, and then quenched with gas.
Ion Nitriding
Ion nitriding is an extension of conventional nitriding processes using plasma discharge physics.
In a vacuum, high-voltage electrical energy is used to form a plasma through which nitrogen ions are accelerated to impinge on the workpiece.
Ion bombardment heats the product, cleans the surface, and provides active nitrogen.
PIT TYPE
Carburizing & Nitriding
Various heat-treating methods are processed in a hermetically sealed, inner-retort pit-type furnace.
High throughput with fair quality for small sizes at a value price. Suitable for heat-treating shaft type of workpiece.
Aluminum Melting Furnace
Low-pressure Aluminum Die-casting Line
Aluminum Melting Furnace
Designed to rapidly melt aluminum ingots or scraps. Capsule-type charging is done automatically, manual transferring of molten aluminum.
+ Raw material using SKIP and CAPSULE
+ Energy saving type (heat recycle)
+ Melting and reserving of ingot/scrap
Aluminum Tilting & Melting Furnace
Design to hold molten aluminum for post-processing.
+ Heavy continuous melting and heat reserving
+ Heat recycle by the heat exchanger
Low Pressure Die
Auto-continuous casting
+ Al WHEEL or CYLINDER HEAD
+ Investment casting
ALUMINUM HEAT TREATMENT
Rotary Type Heat Treatment Furnace
Fully automated rotary furnace using turntable and robot-arm loading and unloading mechanism. The favorable choice for solution treating and aging of large aluminum parts such as cylinder block, cylinder head, and wheels. A gas burner and a large fan in a circular structure improve heat distribution.
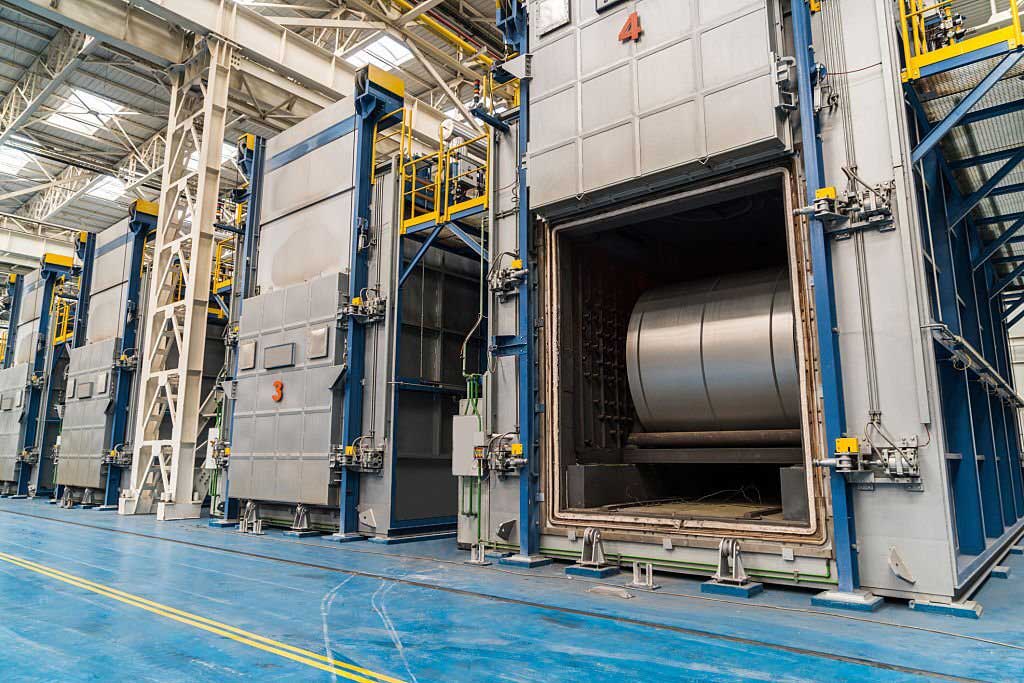
Roller Hearth Type Aluminum heat treatment Furnace
Fully automated roller hearth furnace using stable roller-type loading and unloading mechanism. The favorable choice for solution treating and aging of large aluminum parts such as cylinder block, cylinder head, and wheels.
+ Suitable for mass production
+ T-4, 5, 6, 7 heat treating
STEEL INDUSTRIAL
Continuous Billet Heat Treatment
Car Bottom Heat Treating
ADDITIONAL EQUIPMENT
Endothermic Gas Generator
Endothermic RX gas generator with unique smoke-protecting mechanism has earned many good reviews in various fields.
To generate stable gas, this generator is equipped with a double-pass retort, a special heating device, and a pulseless blower.
Washing Machine
Uses alkaline solution to clean cutting or quenching oil contamination in the pre-and post-process of heat treating. Two-step cleaning operation (dip and spray) with the separated tank (alkaline and warm water), followed by de-oiler.
Tempering Furnace
Low temperature, high temperature, and low and high temperature tempering furnace depending on the target temperature. Stirring fans and special muffles are used for better heat distribution.
Pre-heating Furnace
The pre-heating process also removes oil contamination with a gas-burning (LPG, LNG) mechanism.
COMMERCIAL HEAT TREATMENT DIVISION
CARBURIZING
Gas Carburizing
Carbonitriding hardens the surface of steel by diffusing carbon and nitrogen simultaneously into steel in carburizing atmosphere with ammonia gas at around 850 deg C lower than typical carburizing temperature.
Traditional case-hardening process in which carbon is dissolved in the surface layer of low-carbon steel at a temperature sufficient to render the steel austenitic, followed by quenching and tempering to form martensitic microstructure.
It offers several advantages over carburizing, including low distortion, bigger resistance to softening during tempering, and fatigue strength.
Carbo Nitriding
Traditional case-hardening process in which carbon is dissolved in the surface layer of low carbon steel at a temperature sufficient to render the steel austenitic, followed by quenching and tempering to form martensitic microstructure.
Carbonitriding hardens the surface of steel by diffusing carbon and nitrogen simultaneously into steel in carburizing atmosphere with ammonia gas at around 850℃ lower than typical carburizing temperature.
It has several advantages such as low distortion, bigger resistance of softening during tempering, and fatigue strength over carburizing.
Vacuum Carburizing – Gas Quenching
Non-equilibrium, boost-diffusion carburizing process in which steel being processed is austenitized in a rough vacuum, carburized in partial pressure of hydrocarbon gas, diffused in a rough vacuum, and then quenched with gas.
Vacuum Carburizing – Oil or Salt Quenching
None equilibrium, boost-diffusion carburizing process in which steel being processed is austenitized in a rough vacuum, carburized in partial pressure of hydrocarbon gas, diffused in a rough vacuum, and then quenched With Oil or Salt.
NITRIDING
Gas Nitriding
Case-hardening process that introduces nitrogen into the surface of a solid ferrous alloy by holding the metal at a suitable temperature (below Ac1, for ferritic steels) in contact with a nitrogenous gas, usually ammonia. Does not require quenching for the production of a hard case.
CarboNitriding
Traditional case-hardening process in which carbon is dissolved in the surface layer of low-carbon steel at a temperature sufficient to render the steel austenitic, followed by quenching and tempering to form martensitic microstructure.
Carbonitriding hardens the surface of steel by diffusing carbon and nitrogen simultaneously into steel in carburizing atmosphere with ammonia gas at around 850`c, lower than the typical carburizing temperature.
It offers several advantages over carburizing, including low distortion, greater resistance to softening during tempering, and fatigue strength.
Oxy-Nitriding
Oxynitriding forms Fe3O4 at the outer layer over the compound layer
Ion(Vacuum) Nitriding
Ion nitriding extends conventional nitriding processes using plasma discharge physics. In a vacuum, high-voltage electrical energy is used to form a plasma through which nitrogen ions are accelerated to impinge on the workpiece. Ion bombardment heats the product, cleans the surface, and provides active nitrogen.
QUENCHING & TEMPERING
The heat-treating method in which mid- and high-carbon and structural alloy steel are quenched from austenitic temperature to give martensite structure. Temper below the sub-critical temperature to give certain toughness.
Vacuum
Low vacuum state process using nitrous oxide
INDUCTION HEAT PLUG QUENCHING
Specialized to treat size-sensitive automotive gears. Forced quenching using a plug provides excellent anti-deformation properties and allows selective hardening and toughening in one workpiece.
AUSTEMPRING
“Quench to above Ms point(250˚C ~ 550˚C) from austenitic temp to form bainite.”
Dongwoo Surfacetech (India) Pvt Ltd
Manufacturer of Aluminum Melting Furnace
Plot No: 126, Samathuvapuram,
Ulundai (Post) – 602105
Thiruvallur (TK & Dist)
Tamilnadu, India
+91 44 2769 9814
http://www.dwsi.co.in/index.html
You may also be interested in these furnace manufacturers:

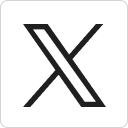




One thought on “Dongwoo Surfacetech”