ATC Tools manufactures a wide range of high-quality cutting tools viz; Solid Carbide Ball Nose Cutters, HSS Drills, End Mills and Solid Carbide HSS Reamers.
The ATC Toolkit offers a comprehensive range of products for various machining needs. This includes special and non-standard tools made from HSS M2, HSS M35, and HSS M42. The toolkit also includes brazed tools and solid carbide tools for different applications.
In addition, the toolkit features solid carbide drills with self-centering capabilities, ensuring precise hole placement. The drills incorporate various geometries such as 4-facet, S-shaped, and X-shaped, providing efficient cutting performance.
The ATC Toolkit also offers tools with a 3-rake cutting edge, enhancing the cutting efficiency and reducing chip formation. Lastly, the toolkit includes special form tools designed to meet specific machining requirements.
Overall, the ATC Toolkit provides a comprehensive selection of high-quality tools to meet various machining needs, ensuring precision, efficiency, and performance.
ATC offers a wide range of center drills and spotting drills designed for centering and spotting applications. Here are some key features and options available:
- Types and Sizes: ATC provides both standard and special types of center drills in different sizes to meet various needs. The available types include Type “A”, Type “B”, and Type “R” center drills.
- Material and Coating Options: Center drills are manufactured using different materials and coatings to enhance their performance. ATC offers HSS (High-Speed Steel) center drills made from materials like HSS M35 (Co%5) and HSS M42 (Co%8). Additionally, solid carbide center drills are available, known for their durability and high cutting performance. Coating options include both coated and non-coated center drills.
- Flatted Body and Oil Groove: Center drills from ATC can be provided with a flatted body or a special flatted body, catering to specific customer requirements. Some center drills also feature an oil groove body for improved lubrication during machining operations.
- Angle Variations: ATC offers 60° center drills, which are commonly used for general centering purposes. Additionally, 60°/120° double angle center drills are available, providing versatility for different applications.
- Special Features: ATC manufactures solid carbide center drills with special coolant holes, allowing for efficient chip evacuation and improved cooling during machining processes.
- Single and Double End: Center drills are available in both single and double end configurations, providing flexibility for various drilling applications.
- Material Options: ATC uses a range of materials for center drills, including HSS M35 (Co%5), HSS M42 (Co%8), ASP30, M2, and solid carbide. These materials offer different levels of hardness, wear resistance, and cutting performance.
In summary, ATC offers a comprehensive selection of center drills and spotting drills to meet different centering and spotting requirements. The range includes various types, sizes, materials, coatings, and special features. ATC’s center drills are designed to provide accurate centering, durability, and efficient chip evacuation for improved machining performance.
Solid Carbide Ball Nose Cutters
Solid carbide ball nose cutters, also known as ball end mills or spherical end mills, are cutting tools specifically designed for machining curved surfaces, 3D contours, and complex shapes in a wide range of materials. They are commonly used in CNC milling and machining operations. Here are some key features and benefits of solid carbide ball nose cutters:
- Construction and Material: Solid carbide ball nose cutters are made from a single piece of solid carbide material. Carbide is a hard and wear-resistant material, making these cutters highly durable and suitable for demanding machining applications. The solid construction ensures stability and precision during the cutting process.
- Spherical Cutting Edge: The cutting edge of a solid carbide ball nose cutter is shaped like a sphere, with a rounded tip. This design allows for smooth and accurate cutting in curved surfaces, intricate contours, and 3D profiles. The ball nose shape enables the cutter to create radiused features and blend transitions between different surfaces.
- Versatility: Solid carbide ball nose cutters are versatile tools that can be used in a wide range of materials, including metals, plastics, composites, and wood. They are capable of machining both soft and hard materials, providing flexibility in various industries such as aerospace, automotive, mold making, and general machining.
- Improved Surface Finish: The spherical cutting edge of solid carbide ball nose cutters helps achieve a superior surface finish on the machined part. The rounded tip reduces the likelihood of chatter or tool marks, resulting in a smoother surface texture. This is particularly important in applications where aesthetics or the reduction of post-processing is crucial.
- Contouring and 3D Machining: Due to their shape and design, solid carbide ball nose cutters excel in contouring and 3D machining operations. They can efficiently remove material along curved paths and produce intricate details, such as fillets, grooves, and pockets. This makes them essential tools for sculpting complex shapes and achieving precise dimensional accuracy.
- High Speed and Feed Rates: Solid carbide ball nose cutters are engineered to withstand high cutting speeds and feed rates. The combination of the robust carbide material and optimized flute design allows for efficient material removal and increased productivity. This makes them suitable for high-performance machining operations.
- Compatibility with CNC Machinery: Solid carbide ball nose cutters are commonly used in computer numerical control (CNC) machining. They are compatible with CNC milling machines and can be programmed to execute complex toolpaths, enabling automation and repeatability in manufacturing processes.
In conclusion, solid carbide ball nose cutters are essential tools for precision machining of curved surfaces, contours, and 3D profiles. Their spherical cutting edge, durability, versatility, and ability to deliver superior surface finish make them indispensable in various industries that require intricate and high-quality machined components.
HSS Drills Solid Carbide HSS Reamers
HSS drills, or High-Speed Steel drills, are a type of cutting tool commonly used for drilling holes in a wide range of materials. Here are some key features and benefits of HSS drills:
- Material Composition: HSS drills are made from a specific type of steel called high-speed steel. This steel alloy is engineered to withstand the high temperatures generated during drilling operations without losing its hardness. It typically contains elements such as tungsten, molybdenum, chromium, and vanadium, which contribute to its strength, toughness, and heat resistance.
- Versatility: HSS drills are versatile tools suitable for drilling in various materials, including metals (such as steel, aluminum, and cast iron), wood, plastics, and composites. They are commonly used in applications ranging from general-purpose drilling to specific industries like automotive, construction, metal fabrication, and woodworking.
- Durability: HSS drills are known for their durability and resistance to wear. The high-speed steel material offers excellent hardness, toughness, and heat resistance, allowing the drills to maintain their cutting performance even under demanding conditions. With proper usage and maintenance, HSS drills can have a long tool life.
- Cutting Performance: HSS drills provide good cutting performance across a wide range of cutting speeds and feed rates. They are capable of producing accurate holes with good surface finish. However, the cutting speeds used with HSS drills are generally lower than those used with other advanced cutting tool materials like carbide.
- Cost-Effectiveness: Compared to some other types of cutting tools, HSS drills are relatively more affordable. This makes them a cost-effective choice for general-purpose drilling applications or when drilling materials that are less abrasive or demanding on cutting tools.
- Compatibility: HSS drills are compatible with various drilling machines, including handheld drills, drill presses, and CNC machines. They come in a wide range of sizes and types, such as twist drills, jobber drills, reduced shank drills, and more, making them suitable for different hole diameters and drilling depths.
- Resharpening: One advantage of HSS drills is their ability to be resharpened. When the cutting edges become dull or worn, HSS drills can be sharpened or reground, extending their useful life and reducing tool replacement costs. This makes them a more economical choice in the long run.
In summary, HSS drills offer versatility, durability, and cost-effectiveness for a wide range of drilling applications. Their high-speed steel composition provides good cutting performance and durability in drilling various materials. While they may not match the performance of more specialized cutting tools in certain applications, HSS drills remain a reliable choice for general-purpose drilling tasks.
When it comes to precision and efficiency in drilling operations, having the right tool for the job is crucial. Today, we will delve into the world of specialized drills, showcasing their unique features and applications. From long series to taper drills with chip breakers, these advanced tools offer unparalleled versatility and performance in various industries.
End Mills Solid Carbide HSS Reamers
End mills are cutting tools used in milling operations to remove material from a workpiece. They are commonly used in CNC milling machines, manual milling machines, and machining centers. Here are some key features and types of end mills:
- Construction and Material: End mills are typically cylindrical in shape with cutting edges on both the end face and the periphery. They are made from various materials, including high-speed steel (HSS), cobalt steel, solid carbide, and sometimes even diamond coatings for specialized applications. The choice of material depends on factors such as the type of material being machined, cutting conditions, and desired tool life.
- Cutting Geometry: End mills come in different geometries to suit specific machining operations and materials. The most common types include:
- Square end mills: Feature a flat cutting end for general-purpose milling, slotting, and profiling.
- Ball nose end mills: Have a rounded end, ideal for 3D contouring, sculpting, and creating smooth curves.
- Corner radius end mills: Have a rounded corner, offering increased strength and better chip evacuation while still maintaining a square profile.
- Roughing end mills: Designed with fewer flutes and a higher chip volume capacity for fast material removal in roughing operations.
- Chamfer end mills: Used for chamfering, beveling, and deburring edges of a workpiece.
- Flute Design: The flute design of an end mill refers to the number, shape, and arrangement of the cutting edges on the tool. Common flute designs include:
- Two-flute end mills: Provide good chip evacuation and are suitable for softer materials and operations requiring high feed rates.
- Four-flute end mills: Offer improved stability, better surface finish, and increased tool life, making them versatile for a wide range of materials.
- Multiple-flute end mills: Have more than four flutes and are useful for specific applications that require higher precision, such as fine detail work or high-speed machining.
- Coatings: End mills can be coated with various coatings to enhance their performance and durability. Common coatings include titanium nitride (TiN), titanium carbonitride (TiCN), aluminum titanium nitride (AlTiN), and diamond-like carbon (DLC). Coatings can provide benefits such as increased hardness, heat resistance, reduced friction, and improved chip evacuation.
- Application: End mills are used in a wide range of machining operations, including face milling, contouring, slotting, profiling, and drilling. They are employed in industries such as aerospace, automotive, mold making, general machining, and more. The specific type of end mill chosen depends on the material being machined, desired surface finish, cutting parameters, and the complexity of the workpiece.
- Compatibility: End mills are compatible with various milling machines, including CNC machines, manual milling machines, and machining centers. They can be used for both roughing and finishing operations, depending on the application and the specific geometry of the end mill.
In summary, end mills are versatile cutting tools used in milling operations to remove material from a workpiece. With a wide range of types, materials, and geometries available, end mills offer flexibility and efficiency in machining applications across different industries. The choice of end mill depends on factors such as the material being machined, the desired surface finish, cutting conditions, and the specific operation being performed.
Solid Carbide Drills
Solid carbide drills are cutting tools used for drilling holes in various materials, including metals, composites, plastics, and wood. They are known for their durability, high cutting performance, and excellent precision. Here are some key features and benefits of solid carbide drills:
- Material Composition: Solid carbide drills are made from a solid piece of carbide, a composite material composed of tungsten carbide particles embedded in a binder material, typically cobalt. Carbide offers exceptional hardness, wear resistance, and heat resistance, making it well-suited for demanding drilling applications.
- Superior Hardness and Wear Resistance: Carbide is significantly harder than high-speed steel (HSS) and other conventional drill materials. This hardness enables solid carbide drills to maintain sharp cutting edges for longer periods, resulting in extended tool life and reduced downtime for tool changes. They are less prone to wear and can withstand higher cutting speeds and feed rates.
- Enhanced Cutting Performance: Solid carbide drills deliver high cutting performance, allowing for increased productivity and efficiency. They exhibit excellent chip evacuation capabilities, reducing the risk of chip clogging and improving drilling stability. The sharp and rigid cutting edges of solid carbide drills ensure precise hole diameters and superior surface finishes.
- Versatility: Solid carbide drills can be used in a wide range of materials and applications. They are particularly effective for drilling hard materials such as stainless steel, cast iron, titanium alloys, and hardened steels. They are also suitable for drilling softer materials, including aluminum, copper, plastics, and composites. This versatility makes them ideal for various industries, such as aerospace, automotive, mold making, and general machining.
- Compatibility with High-Speed Machining: Solid carbide drills are compatible with high-speed machining processes, enabling faster drilling speeds and feed rates. They can effectively handle the demands of high-performance machining, where rapid material removal and increased productivity are required.
- Stability and Accuracy: Due to their rigid construction and superior cutting properties, solid carbide drills offer excellent stability and accuracy during drilling operations. They are designed to minimize deflection and vibration, resulting in precise hole placement and dimensional accuracy. This makes them suitable for applications that require tight tolerances and exact hole sizes.
- Compatibility with CNC Machinery: Solid carbide drills are commonly used in computer numerical control (CNC) machines, where their high cutting performance and precision are maximized. They can be programmed to execute complex drilling operations, such as deep hole drilling, angled drilling, and hole patterns, with consistent and reliable results.
In summary, solid carbide drills are highly durable and efficient cutting tools used for drilling holes in various materials. Their exceptional hardness, wear resistance, and cutting performance make them suitable for demanding drilling applications. Solid carbide drills offer versatility, stability, and accuracy, contributing to increased productivity and superior hole quality in machining operations.
Long Series Drills
Long series drills are designed for deep drilling applications, providing extended reach and stability. They are commonly used in industries such as aerospace, automotive, and oil and gas, where drilling through thick materials or reaching inaccessible areas is essential. With their extended length, long series drills enable efficient and accurate drilling even in challenging circumstances.
Deep-hole V63 Type Drills
Deep-hole V63 type drills are specifically engineered for deep-hole drilling tasks. These drills feature a unique flute design that optimizes chip evacuation, reducing the risk of chip clogging and improving drilling efficiency. The V63 design allows for enhanced coolant flow, ensuring efficient cooling and lubrication during prolonged drilling operations. Industries such as mold making, medical equipment manufacturing, and firearm production benefit greatly from these specialized drills.
Quick Spiral Drills Solid Carbide HSS Reamers
Quick spiral drills, as the name suggests, have a steep helix angle that enables rapid chip evacuation. They are ideal for drilling in softer materials, such as wood, plastics, and non-ferrous metals. The quick spiral design minimizes heat buildup and improves chip control, resulting in smoother drilling and reduced chances of work piece damage. Quick spiral drills are commonly used in woodworking, signage production, and electrical installations.
Extra Long Drills
Extra-long drills are designed to reach deep or hard-to-access areas. With their extended length, these drills offer increased flexibility and maneuverability. They are widely used in applications such as plumbing, electrical conduit installation, and architectural metalwork, where drilling through thick walls or tight spaces is required. Extra-long drills provide the necessary reach without compromising accuracy and precision.
Sub-land Drills Solid Carbide HSS Reamers
Sub-land drills are engineered with multiple cutting edges and specialized geometries to enhance stability and accuracy during drilling operations. These drills excel in challenging materials such as stainless steel, heat-resistant alloys, and hardened steels. The sub-land design reduces cutting forces, minimizes vibration, and extends tool life. Industries like aerospace, automotive, and energy generation heavily rely on sub-land drills for their demanding drilling requirements.
Delta Drills Solid Carbide HSS Reamers
Delta drills, also known as indexable insert drills, offer excellent productivity and cost-efficiency. These drills feature replaceable cutting inserts that allow for quick and easy tool changes, reducing downtime and increasing efficiency. Delta drills are commonly used in mass production environments, where high volumes of holes need to be drilled rapidly. They are widely employed in industries such as automotive manufacturing, aerospace assembly, and general machining.
Spade Drills Solid Carbide HSS Reamers
Spade drills, also known as flat wood bits, are designed for drilling larger diameter holes in materials like wood, plastic, and thin metals. They feature a flat, paddle-shaped cutting edge that efficiently removes material, leaving behind a clean, flat-bottomed hole. Spade drills are commonly used in woodworking, construction, furniture making, and general fabrication tasks. Their versatility and ease of use make them popular among both professionals and DIY enthusiasts.
Cone Drills (Step Drills) Solid Carbide HSS Reamers
Cone drills, also referred to as step drills, are renowned for their ability to create holes with different diameters using a single tool. These drills have multiple steps with progressively increasing diameters, allowing users to drill holes of various sizes without changing the tool. Cone drills are particularly useful in sheet metal fabrication, electrical installations, plumbing, and HVAC applications. They eliminate the need for multiple drill bits and reduce setup time, improving overall efficiency.
Taper Drills with Chip Breaker
Taper drills with chip breakers are specifically designed to enhance chip evacuation and prevent chip entanglement during drilling operations. The chip breaker, located on the cutting edge, breaks up the chips into smaller, manageable pieces, improving chip flow and reducing the risk of clogging. These drills are commonly used in metalworking applications, especially when drilling into materials like stainless steel, cast iron, and aluminum. Taper drills with chip breakers help maintain cutting performance, extend tool life, and ensure smooth and reliable drilling results.
Solid Carbide HSS Reamers
Reamers are cutting tools used for enlarging, shaping, and improving the accuracy of existing holes. They are designed to remove a small amount of material from the interior surface of a hole, resulting in a precisely sized and finished hole. Here are some key features and benefits of reamers:
- Hole Accuracy and Surface Finish: Reamers are used to achieve precise hole dimensions and improved surface finish. They remove any irregularities, burrs, or misalignments left from the drilling or machining process, resulting in a smooth, accurately sized, and properly aligned hole. Reaming ensures that the hole meets specific tolerance requirements, enabling better fitting of mating parts or components.
- Types and Designs: There are various types and designs of reamers, each suited for specific applications and materials. Common types include:
- Hand reamers: Designed for manual operation, typically with a square end or a tang for use with a tap wrench or handle.
- Machine reamers: Designed for use in drilling machines, lathes, or milling machines, with features such as straight shanks or taper shanks for easy installation in machine tool chucks.
- Tapered reamers: Have a gradual taper along their cutting edges, enabling them to produce tapered holes or countersinks.
- Adjustable reamers: Feature adjustable blades or cutters that can be expanded or contracted to achieve different hole sizes.
- Chucking reamers: Have a straight shank and are designed to be held in a chuck or collet for precise machining operations.
- Material Compatibility: Reamers can be used in various materials, including metals (such as steel, aluminum, brass, and cast iron), wood, plastics, and composites. Different reamer designs and cutting geometries are available to optimize performance and tool life for specific materials.
- Size Range: Reamers are available in a wide range of sizes, allowing for hole enlargement from small diameters to larger dimensions. They come in both standard and metric sizes, making them suitable for different measurement systems.
- Cutting Action: Reamers typically have multiple cutting edges along their cylindrical or conical surfaces. They remove material gradually and evenly as they rotate and move through the hole, producing a more accurate and consistent hole diameter compared to drilling alone. Reamers can have straight or spiral flutes to aid in chip evacuation.
- Compatibility with Existing Holes: Reamers are specifically designed to work with pre-drilled or pre-machined holes. They can be used to improve the accuracy and finish of holes created by drilling, boring, or other machining operations. By selecting the appropriate reamer size and design, the existing hole can be brought to the desired dimensions and quality.
- Resharpening and Reuse: In many cases, reamers can be resharpened or refurbished, extending their useful life and reducing tool replacement costs. This is particularly beneficial for high-quality or specialized reamers. Resharpening restores the cutting edges and maintains the original accuracy and performance of the reamer.
In summary, reamers are cutting tools used for precision hole enlargement and improvement of hole accuracy and surface finish. They are available in various types, sizes, and designs to accommodate different applications and materials. Reaming is an essential process in machining, allowing for precise hole sizing, alignment, and improved fit of components.
ATC TOOLS PRIVATE LIMITED
Developed Plot No: 123,
13th Main Road, Sidco Industrial Estate,
Thirumudivakkam, Chennai-600044
044 – 64601243, 42846147
You may also be interested in this manufacturer of Austempered Ductile Iron Castings:

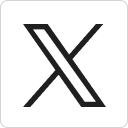




One thought on “ATC Tools”